К шасси автомобиля относятся узлы и агрегаты трансмиссии (сцепление, коробка передач, карданная передача и задний мост), ходовой части (передняя и задняя подвеска) и механизмов управления (рулевого и тормозов). Именно так мы их и рассмотрим.
Данная последовательность рассмотрения агрегатов шасси позаимствована из принятой в курсах устройства автомобиля ещё с 1930-х гг. так называемой «силовой» схемы: агрегаты рассматриваются в том порядке, в котором через них передаётся усилие от двигателя. «Силовую» схему изучения устройства автомобиля активно критиковали ещё с 1960-х годов как не соответствующую базовому принципу педагогики — «от простого к сложному»; однако, данный текст не является учебным пособием, поэтому не будем нарушать сложившейся традиции.
Шасси «Волги» ГАЗ-24 было разработано в начале 1960-х годов полностью с нуля, с широким использованием многих наработок и отдельных деталей от автомобиля более высокого класса ГАЗ-13 «Чайка». В подвеске из общего с предыдущей «Волгой» ГАЗ-21 осталась только общая схема (шкворневая независимая подвеска на двойных поперечных рычагах спереди, рессорная зависимая сзади), а напрямую от неё перешли лишь тормозные механизмы (за исключением «начинки» рабочих цилиндров, которые стали «самоподводящимися», и механизма стояночного тормоза).
В общем, если какие-либо из применённых в волговском шасси технических решений и выглядят архаичными с современной точки зрения, вроде шкворневой передней подвески — то это было следствием осознанного выбора, сделанного разработчиками данной конструкции, а не унификации с более ранними моделями. Нужно помнить, что в случае «Волги» ГАЗ-24 мы имеем дело с инженерными компромиссами образца середины шестидесятых годов, которые с точки зрения современного автовладельца, привыкшего к автомобилям совершенно иного технического уровня, могут выглядеть глупо и нелепо, но на самом деле были на тот момент вполне актуальны, причём в масштабе всего мирового автопрома.
Сцепление — сухое, однодисковое, пружинно-рычажного типа: с шестью периферийными цилиндрическими нажимными пружинами, тремя рычажками включения («лапки») и ведомым диском диаметром 225 мм.
Конструкция не самая передовая на тот момент — например, с 1967 года на «Москвиче-412» уже ставилось лицензионное сцепление с диафрагменной нажимной пружиной Бельвилля, более простое по устройству, не требующее регулировки и с более комфортной работой — как и на «Жигулях». Тем не менее, вполне адекватная своему назначению.
Аналогичные конструкции применялись в те годы и за рубежом, к примеру — на легковых автомобилях концерна Chrysler с рядной «шестёркой» очень похожие пружинно-рычажные сцепления марки Borg&Beck устанавливались до начала 80-х годов, а на пикапы и внедорожники — до конца того же десятилетия. На тяжёлых грузовиках и спецтехнике сцепления данного типа используются до сих пор.
Главные преимущества диафрагменного сцепления — меньшее усилие и меньший рабочий ход диска, что позволяет спроектировать более комфортный привод с меньшим ходом педали и/или меньшими усилиями на ней. Кроме того, в нём отсутствуют детали, требующие регулировки, периодического обслуживания или замены (оно заменяется только всё в сборе). При этом оно хуже работает при больших нагрузках и высоких оборотах, поэтому на грузовиках и внедорожниках, а также автомобилях с форсированными моторами, его применяли редко (в настоящее время эта проблема отчасти решена), а также менее долговечно (фактически — должно заменяться в сборе при каждой замене ведомого диска, так как они спроектированы и изготовлены как единый узел и должны заменяться именно комплектом).
Рычажное сцепление при регулярном уходе является практически «вечным» (зафиксированы пробеги 300 тыс. км и более без каких либо вмешательств) — при должном качестве изготовления его «корзина» (нажимной диск) выхаживает сравнимо с ресурсом самого автомобиля. При перегреве ведомого диска цилиндрические пружины, в отличие от диафрагменной, как правило не «садятся», так как под них подложены теплоизоляционные шайбы, предохраняющие их от нагрева выше температуры отпуска стали. При износе «лапок» их можно заменить на новые, так что корзину целиком менять не приходится (у более ранних машин ГАЗ ещё и сами «лапки» имели рабочую регулировку за счёт выполненных в виде винтов контактных площадок на их концах, однако, видимо, её посчитали избыточной). Кроме того, замена пружин потенциально позволяет конечному пользователю регулировать усилие прижима диска, и за счёт этого в какой-то степени усиливать сцепление для работы с форсированными моторами.
Разумеется, на практике все как правило, пользуясь «неубиваемостью» агрегата, дружно «забивают» на его обслуживание — результатом чего становятся корзины с таки «убитыми» отсутствием смазки в течение десятилетий игольчатыми подшипниками лапок, как следствие «гуляющие» как им вздумается при каждом выжиме; в итоге — неустранимый дисбаланс, дёрганье при трогании, и т.п. труднодиагностируемые неисправности, которые сваливают на всё что угодно, кроме их первопричины.
На самом деле, если перебрать такую корзину — заменить лапки (на соответствующие по качеству: напильник должен еле царапать рабочую поверхность), заложить в их подшипники современную смазку с длительным сроком службы, проточить нажимную плиту (минимальная допустимая толщина 15,6 мм) и отрегулировать её величину выжима — она вполне может проходить ещё столько же, сколько уже прошла (а это в большинстве случаев весь срок службы автомобиля).
Ещё одна причина рывков — поведённая от очень сильного перегрева нажимная плита. Но тут вопросы должны возникнуть уже к тому, кто эксплуатировал машину, и вопросы очень серьёзные.
Существенным недостатком конкретной реализации рычажного сцепления на «Волге» (и всех автомобилях ГАЗ тех лет) было то, что его ведущий диск («корзина») с технологической точки зрения представлял собой часть коленчатого вала конкретного двигателя, балансировалась вместе с ним и по сути не подлежала замене в процессе эксплуатации, так как при этом требовалось заново балансировать коленвал в сборе с маховиком и «корзиной». Однако на практике существенной проблемой это как правило не становилось, так как полная замена «корзины» сцепления, кроме как при капитальном ремонте автомобиля в заводских условиях, требовалась крайне редко.
Руководство по капремонту автомобиля, к примеру, вообще не рассматривало случая выбраковки ведущего диска сцепления в сборе; предусматривалась только замена отдельных его элементов — нажимной плиты, рычагов, пружин — при наличии у них серьёзных механических повреждений. Собственно, предприятия, осуществлявшие капремонт автомобилей, как раз имели и оборудование для балансировки коленчатых валов в сборе со сцеплением.
Существенных изменений этот агрегат на протяжении выпуска автомобилей 24-того семейства не претерпел, успешной перейдя по наследству семейству 3102-31029, и даже некоторым экземплярам ГАЗ-3110 первых выпусков (примерно с 1998 года на часть машин с «402-м» мотором уже ставилось «лепестковое» сцепление от «406-го», с диафрагменной нажимной пружиной и увеличенным до 240 мм ведомым диском).
Гидравлический привод выключения сцепления менялся один раз — в 1974 году.
До этого на ГАЗ-24 использовался рабочий цилиндр сцепления от ГАЗ-21, имеющий шток из двух частей с регулировкой длины. Между внешней обоймой выжимного подшипника и рычагами «корзины» сцепления поддерживался постоянный (регулируемый длиной штока) зазор в 2,5 мм. При нажатии на педаль сначала выбирался этот зазор, и только после этого выжимной подшипник касался рычагов «корзины» сцепления и начинался его рабочий ход. При отпущенной педали муфта выключения сцепления специальной пружинкой, расположенной внутри «колокола» сцепления, оттягивалась назад, а другая пружина оттягивала вилку выключения сцепления и таким образом возвращала поршень рабочего цилиндра в исходное положение, поддерживая установленный регулировкой зазор.
За счёт этого выжимной подшипник при отпущенной педали «отдыхал» и вращался только непосредственно в момент выключения сцепления, за счёт чего почти не изнашивался. Однако за это преимущество приходилось платить слишком большим количеством недостатков. Во-первых — при каждом выжиме педали сцепления муфта билась о вращающиеся вместе с маховиком двигателя рычаги «корзины», вызывая ударные нагрузки в приводе. Во-вторых — система требовала пусть и не частой (раз в 20...30 тыс. км), но всё же постоянной регулировки, компенсирующей износ ведомого диска сцепления. В-третьих — действия водителя при переключении передач должны были быть предельно отточенными, в частности — было категорически недопустимо задерживать ногу на педали сцепления (например, чтобы машина продолжала катиться при включенной передаче), что приводило к быстрому износу выжимного подшипника, не рассчитанного на постоянную работу — выключать сцепление допускалось только непосредственно в сам момент переключения передачи или включения «нейтрали», после чего следовало сразу же отпускать педаль, и ни в коем случае не держать её в «полувыжатом» состоянии. При движении в плотном потоке транспорта обеспечить такой режим работы мог только очень дисциплинированный водитель, да и то ценой повышенной утомляемости. На практике же, водители, особенно неопытные «автолюбители» (автовладельцы-частники), то и дело нарушали это правило, что приводило к ускоренному износу узлов сцепления и частым ремонтам.
К середине 1970-х годов появились новые, более совершенные смазочные материалы, которые позволили создать необслуживаемый выжимной подшипник постоянного зацепления ГПЗ-76-360710 АУС9 (24-1601072), в который на заводе закладывалась специальная, очень долговечная синтетическая смазка, рассчитанная на весь срок службы данного узла. Это позволило модернизировать привод сцепления «Волги», сделав его более надёжным и не требующим регулировок и прочего обслуживания.
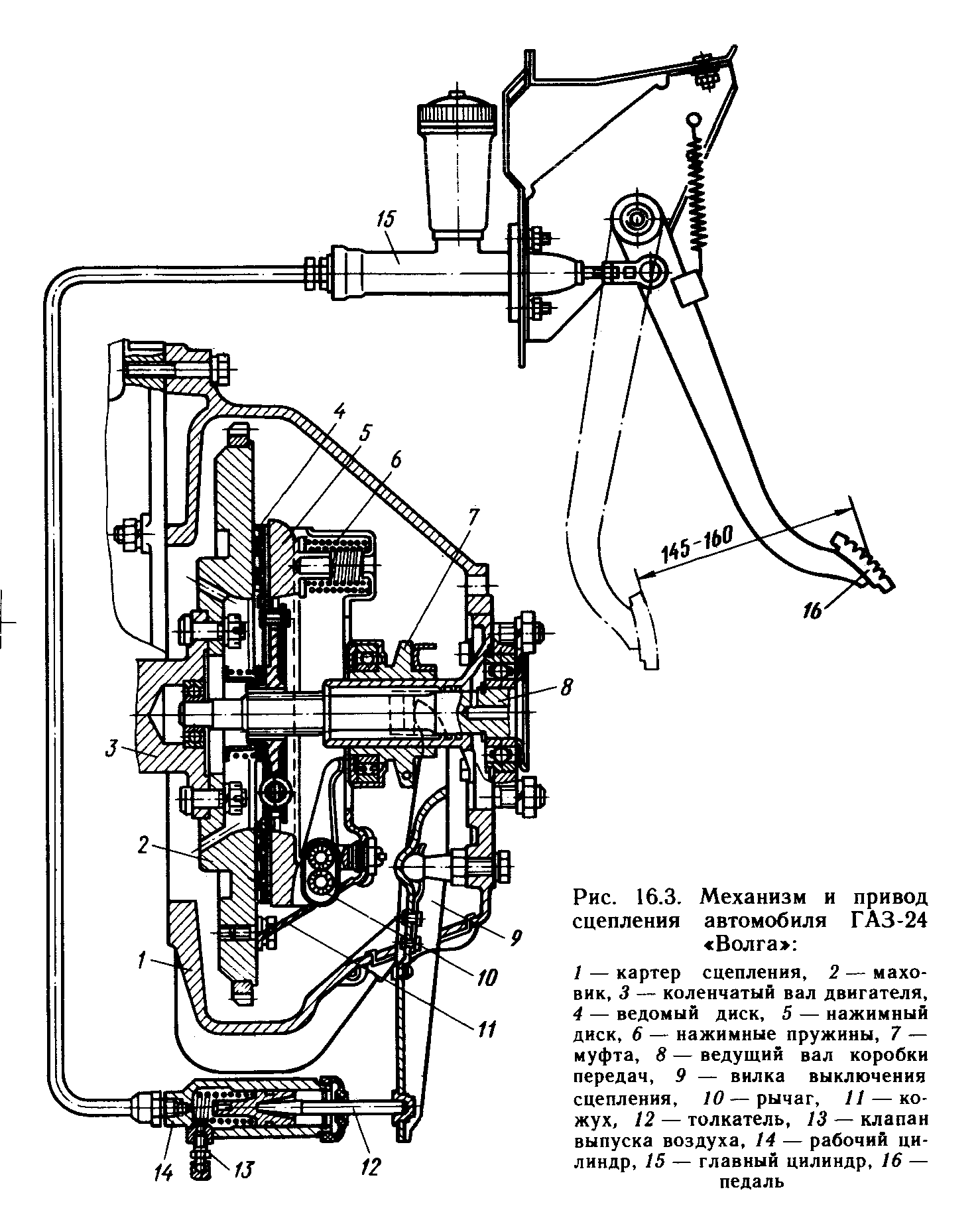
Модернизированный необслуживаемый привод сцепления. Рабочий ход педали в 145...160 мм поддерживался автоматически, все зазоры из привода были устранены.
На ГАЗ-24 с модернизированным приводом сцепления внешняя обойма выжимного подшипника постоянно находится в контакте с рычагами «корзины» за счёт того, что поршень рабочего цилиндра сцепления постоянно поджимается расположенной внутри последнего достаточно мощной пружиной. Через поршень это усилие передаётся на шток рабочего цилиндра, а затем через вилку выключения сцепления — на муфту выключения сцепления с выжимным подшипником, прижимая его к рычагам «корзины». При этом у выжимного подшипника «отобрали» штауферную маслёнку, имевшуюся на ГАЗ-21 и сохранявшуюся на грузовиках ГАЗ, однако в сам подшипник при этом стали закладывать современную смазку с дисульфидом молибдена, не требовавшую замены или пополнения в течение всего срока службы узла (по другой информации — синтетическую полиэфирную смазку ЛЗ-31 с противоокислительной и противокоррозионной присадками; по каталогу подшипников туда идёт именно эта смазка, так что скорее всего в руководстве просто допущена ошибка в обозначении её типа).
Это позволило избежать ударных нагрузок на подшипник при работе сцепления, а главное — устранило всякую необходимость регулировки, так как компенсация износа ведомого диска в такой конструкции происходит автоматически: по мере его износа пружина просто чуть больше выталкивает шток рабочего цилиндра наружу. Так как использованный выжимной подшипник рассчитан на постоянный режим работы, значительного сокращения его ресурса не произошло, а по факту он скорее даже вырос, поскольку новый подшипник был рассчитан на постоянное вращение (да и нагрузка на него при работе «вхолостую» была не особо большой). Кроме того, рабочий ход педали сцепления стал меньше. Ну, а весь уход за приводом сцепления теперь свёлся к поддержанию уровня тормозной жидкости в бачке на главном цилиндре.
Интересно, что на заднеприводных «Москвичах» вместо нормального выжимного подшипника использовался унаследованный ещё от довоенного «Опеля» графитовый вкладыш, который принципиально не мог работать в постоянном режиме. Поэтому на «Москвичах» привод сцепления продолжал требовать тщательной регулировки даже после перехода на новомодную лепестковую «корзину» с диафрагменной пружиной — в противном случае графитовая вставка муфты выключения сцепления (подпятник) изнашивалась очень быстро. На автомобилях ГАЗ же всегда (ещё с довоенных лет) использовался полноценный выжимной подшипник.
Коробка передач ГАЗ-24 представляла собой вполне современный на тот момент агрегат, с алюминиевым картером и четырьмя полностью синхронизированными передачами переднего хода. Крышка — верхняя, а не боковая, как на «Победе», ГАЗ-21 и 69, что позволило увеличить жёсткость картера, более удобно расположить рычаг практически по центру трансмиссионного тоннеля (а не с сильным смещением к месту водителя — влево, как на ГАЗ-69, или вправо как на праворульной ГАЗ-21П с напольным рычагом) и устранить подтекание масла через отверстия в ней.
Механизм выбора передач — трёхходовой, то есть, имеет три ползуна и три вилки, из которых две перемещают муфты включения передач переднего хода с синхронизаторами, а третья, крайне левая — только скользящую шестерню заднего хода. Потенциально при трёхходовом механизме выбора передач можно иметь шесть передач (по две на ползун): пять переднего хода и одну — заднего, но, как мы видим, в данном случае фактически из них были реализованы только пять (4+1), чего было по тем временам вполне достаточно — эпоха массового использования пятой повышающей передачи придёт существенно позже. Привод переключения передач — очень простой и надёжный, с рычагом, непосредственно взаимодействующим своим наконечником с ползунами.
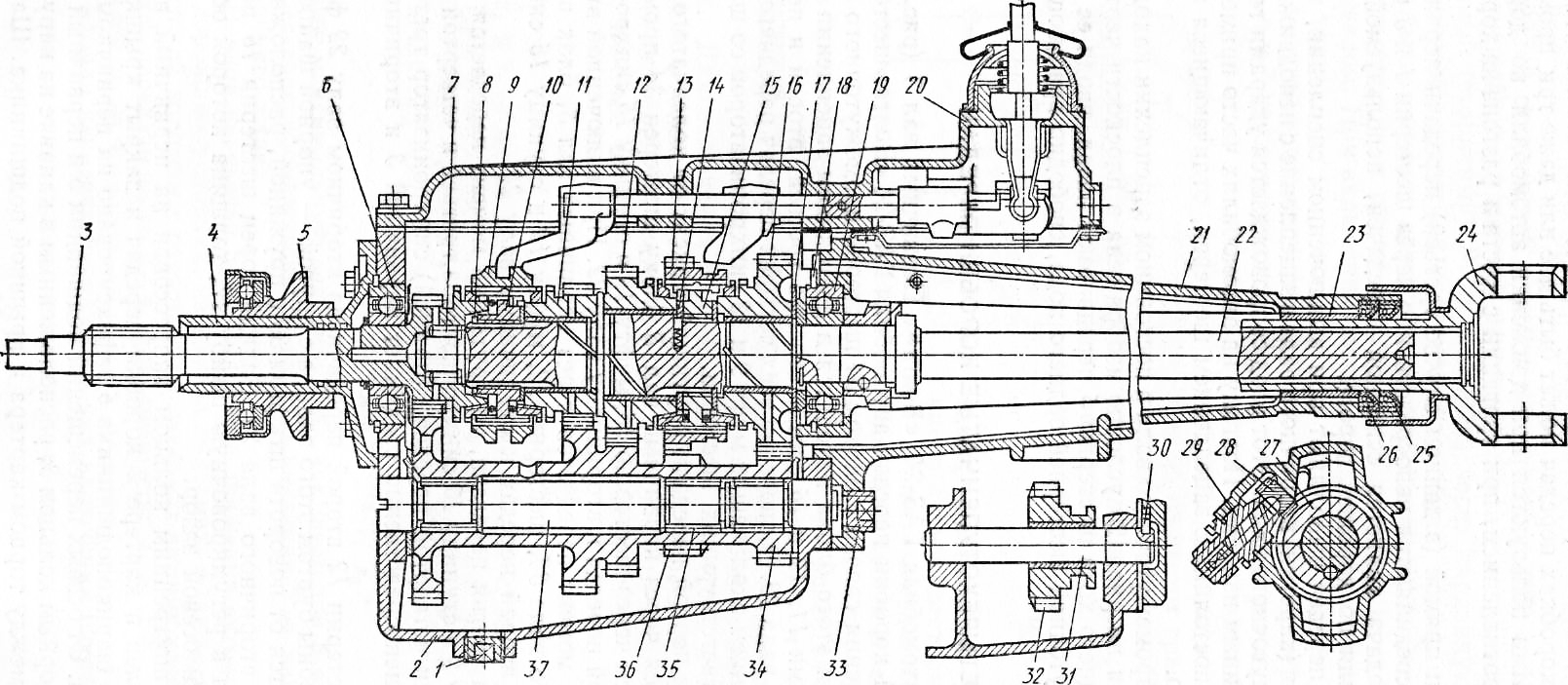
1 — пробка отверстия для слива масла; 2 — картер коробки передач; 3 — первичный вал; 4 — крышка подшипника первичного вала; 5 — муфта выключения сцепления; 6 — задний подшипник первичного вала; 7 — роликовый подшипник; 8 и 18 — стопорные кольца; 9 — муфта синхронизатора третьей и четвертой передач; 10 — ступица синхронизатора третьей и четвертой передач; 11 — шестерня третьей передачи; 12 — шестерня второй передачи; 13 — муфта синхронизатора первой и второй передач; 14 — упорная шайба; 15 — ступица синхронизатора первой и второй передач; 16 — шестерня первой передачи; 17 — регулировочная шайба; 19 — шарикоподшипник; 20 — верхняя крышка коробки передач; 21 — удлинитель коробки передач; 22 — вторичный вал; 23 — сталебаббитовый подшипник скольжения; 24 —скользящая вилка карданного вала; 25 и 26 — сальники; 27 — ведущая шестерня привода спидометра; 28 — ведомая шестерня привода спидометра; 29 — штуцер ведомой шестерни привода спидометра; 30 — штифт; 31 — ось промежуточной шестерни заднего хода; 32—промежуточная шестерня заднего хода; 33 — пробка; 34 — блок шестерен промежуточного вала; 35 — игольчатый подшипник промежуточного вала; 36 шестерня заднего хода; 37 — ось промежуточного вала.
Благодаря отсутствию длинных передаточных тяг передачи на не изношенном агрегате переключаются очень чётко и внятно. У коробок советского выпуска синхронизаторы работали также весьма чётко, все передачи включались без хруста и с умеренными усилиями.
Ещё одна характерная конструктивная особенность коробки — длинный удлинитель картера в его задней части, позволяющий вынести точку крепления карданного вала далеко назад. Это решение связано с применением на автомобиле однозвенного карданного вала, длину которого требовалось как можно сильнее уменьшить. Карданный вал с коробкой передач жёстко никак не связан, он просто свободно скользит на шлицах вторичного вала внутри удлинителя, благодаря чему его снятие и установка значительно упрощены.
Изменения в конструкции коробки на протяжении всего выпуска сводились главным образом к повышению её и без того немалого ресурса за счёт введения новых, улучшенных по конструкции и качеству изготовления компонентов. Так, с конца 1975 года стали устанавливаться блокирующие кольца синхронизаторов новой конструкции, латунные вместо бронзовых, а с августа 1977 года были немного изменены вторичный вал коробки передач, комплект шестерён I передачи и сама шестерня I передачи. С февраля 1978 года были внедрены шестерни II и III передач повышенного качества без бронзовых втулок, и так далее.
К сожалению, в пост-перестроечные годы отвратительно упавшее качество изделий ЗКС (филиал и ближайший сосед ГАЗ-а, Завод коробок скоростей) полностью дискредитировало этот дубовый и в целом весьма надёжный агрегат. В частности, на многих коробках выпуска тех лет отмечались большие проблемы с синхронизацией — вплоть до необходимости вспоминать о приёмах двойного выжима и перегазовки для нормального переключения передач, да и с надёжностью и долговечностью также были проблемы. Впоследствии качество несколько выправилось, но ещё долго продолжало хромать на обе ноги даже, перейдя по наследству и к полностью новой пятиступенчатой коробке — рецедивы «хрустящей болезни» встречались и в 2000-х...
Передаточные числа коробки передач ГАЗ-24 (24-10, 3102): I передача — 3,5; II — 2,26; III — 1,45; IV — 1,0; задний ход — 3,54.
Ранее на автомобили ГАЗ устанавливали трехскоростные коробки передач с синхронизаторами на II и III передачах — ещё со времен «Победы» (с 1950 года); первая передача на тех коробках была не синхронизирована, и быстро включить ее было не всегда возможно.
Трёхскоростные коробки верой и правдой служили автомобилистам в течение десятилетий, до тех пор, пока в середине-конце пятидесятых плотность движения на дорогах не выросла до такой степени, что трёх передач перестало хватать для нормального движения в потоке. Тогда наметился переход к четырёхступенчатым коробкам передач, имевшим две промежуточные передачи вместо одной. Это позволило ощутимо улучшить динамические качества автомобилей, а также, несмотря на некоторое увеличение количества движений рычага коробки, повысить удобство управления автомобилем.
Так, при движении на подъёме или обгоне водитель автомобиля с трёхступенчатой коробкой передач был вынужден оставаться на третьей-прямой передаче, поскольку передаточное число следующей — второй — передачи было излишне высоко, и максимальная скорость на ней была ограничена 60-70 км/ч, что делало её бесполезной при движении на трассе. При этом тяги двигателя часто не хватало для преодоления подъёма, в результате чего автомобиль, несмотря на полностью открытый дроссель, начинал терять скорость. При движении в городской толчее передаточное число второй передачи трёхступенчатой коробки, вынужденно подобранное «на все случаи жизни», оказывалось уже излишне низким, что вынуждало водителя либо мириться с «тупостью» автомобиля и плохой динамикой, либо для резкого ускорения переключаться на первую передачу, что было сопряжено со значительными трудностями ввиду отсутствия на ней синхронизатора, а также излишне нагружало двигатель, поскольку её передаточное число обычно делали очень высоким, в расчёте на трогание на грунте с большим сопротивлением или с тяжёлым грузом.
Введение двух промежуточных ступеней вместо одной элегантно решало обе проблемы. Вторая передача с более высоким передаточным числом, чем у прежней «универсальной» второй, служила для постоянного движения на невысокой скорости в городских условиях, а более «низкая» третья, позволяющая разгоняться до 80...90 км/ч — для энергичного ускорения и обгона на трассе. Улучшалась также и топливная экономичность, так как стало легче подобрать передаточное число трансмиссии, соответствующее текущему режиму движения и обеспечивающее оптимальное число оборотов двигателя.
В особенной степени описанные выше проблемы проявлялись на малолитражных автомобилях, двигатели которых в те годы не обеспечивали высоких тягово-сцепных качеств. Поэтому на «Москвиче» четырёхступенчатая КПП появилась ещё в конце пятидесятых. Более эластичный и тяговитый двигатель «Волги» позволял до поры до времени обходиться тремя передачами, но и в его случае внедрение более совершенной коробки позволило весьма заметно улучшить динамические качества автомобиля и удобство управления.
Управление коробкой напольным рычагом тоже было в новинку тогдашним водителям: ещё со времен второго поколения «Победы» передачи на советских автомобилях, за вычетом «Запорожца», переключались рычагом на рулевой колонке. Однако после появления «Жигулей», быстро ставших одним из наиболее массовых легковых автомобилей в СССР, водители настолько привыкли к напольному переключению коробки передач, что любые другие варианты стали казаться редкой экзотикой — хотя и в США, и в Европе, и в Японии механические коробки передач с подрулевым рычагом продолжали использоваться ещё в восьмидесятые годы, а на отдельных моделях и в девяностые.
Карданная передача — открытая, однозвенная, в отличие от кардана ГАЗ-21 с его двумя валами и промежуточной опорой. Введение такой конструкции позволило сэкономить один карданный шарнир, сделать узел ощутимо более долговечным благодаря устранению из конструкции промежуточной опоры с резиновой вставкой и подшипником, а также существенно упростить работу по снятию карданного вала, при этом одновременно был введён удлинитель на картере коробки передач, позволивший минимизировать длину карданного вала и снизить уровень вибраций. К удлинителю карданный вал крепится через шлицевое соединение, позволяющее компенсировать изменение его длины в ходе работы подвески. Для снятия кардана достаточно отсоединить задний карданный шарнир от фланца главной пары заднего моста — передний конец просто вытаскивается из удлинителя коробки передач. В общем — для своего времени данное решение выглядело в целом удачным.
На автомобилях, выпущенных до 1976 года, иногда проявлялся дефект, связанный с возникновением сильной вибрации и сопровождающего её заметного шума при движении на прямой передаче в диапазоне скоростей 120-130 км/ч. Это происходило из-за того, что при частоте обращения коленчатого вала двигателя в 3 800...4 200 оборотов в минуту вся трансмиссия входила в резонанс. Помимо дискомфорта для водителя и пассажиров, это также уменьшало долговечность агрегатов автомобиля, а в особенно запущенных случаях — даже вело к их поломкам, например трещинам и даже разрушению удлинителя (хвостовика) коробки передач.
В 1976 году была внедрена эластичная резиновая муфта в удлинителе коробки передач и новая задняя опора силового агрегата, что позволило полностью устранить этот дефект и связанные с ним проблемы при эксплуатации. Небольшая безобидная вибрация при скорости около 80 км/ч временами всё же проявляла себя, так как резонанс теперь возникал уже в диапазоне 2 600—2 800 оборотов в минуту — завод объяснял её появление тем, что на на отдельных автомобилях имели место повышенные дисбаланс карданного вала и коленчатого вала двигателя и биение посадочных мест для карданного вала на коробке передач и заднем мосту — но, во всяком случае, поломками она уже не угрожала.
На поздних выпусках ГАЗ-24-10 эластичную муфту убрали, видимо посчитав, что после принятых мер изначальная причина дефекта — дисбаланс деталей трансмиссии и биение посадочных мест — устранена.
Тем не менее, однозвенный кардан ГАЗ-24 всё же имеет одну гадливую особенность, а именно — при езде по неровным дорогам он сильно провисает относительно кузова и часто «цепляет» камни и прочие неровности, от чего на нём появляются вмятины и его балансировка постепенно ухудшается — вплоть до появления разрушительных вибраций, избавиться от которых можно только новой балансировкой или заменой на отбалансированный на заводе новый. Для двухзвенного кардана это свойственно в меньшей мере, так как он неподвижен на участке между коробкой передач и промежуточной опорой и в целом лучше защищён кузовом (хотя и у него имеются свои проблемы, в основном с промежуточной опорой и шлицевым соединением — причём когда первая выходит из строя, очень быстро разбивает и шлицы).
Так или иначе, впоследствии на ГАЗ-3110 всё же вернули двухзвенный кардан с промежуточной опорой (правда, конструкция её была существенно изменена по сравнению с ГАЗ-21, став намного более простой и надёжной).
Каждый подшипник шарнира карданного вала представлял собой своего рода миниатюрный герметичный картер с двойными уплотнениями сальникового типа (радиальным и торцевым), заполненный до середины иголок жидким маслом, которое использовалось для смазывания их подшипников по так называемой поточной системе. Этого запаса масла должно было хватить на весь срок между ТО. На заводе для заполнения подшипников крестовин использовалось густое авиационное моторное масло марки МС-20 или МК-22 с вязкостью примерно SAE 50.
Одновременно с заменой масла в двигателе крестовины предписывалось прошприцевать тем же авиационным маслом или «трансмиссионкой», чтобы пополнить запас смазки, причём на первом ТО «тугие» не приработавшиеся сальники подшипников крестовин нередко не давали нагнетаемому маслу выйти наружу — в таком случае смазывание откладывалось до следующего ТО.
Использование густых (консистентых) смазок категорически воспрещалось, «так как густая смазка не доходит до иголок подшипников карданных шарниров» и «применение таких смазок приводит к разрушению игольчатых подшипников». (фразы из руководств к автомобилям ГАЗ с такими крестовинами).
Выбрасывание некоторого количества масла из шарнира при движении автомобиля, в особенности в первое время после шприцевания крестовин, считалось совершенно нормальным явлением — выбрасывалось только излишнее масло, оставшегося в подшипниках количества было вполне достаточно для нормального смазывания в течение всего срока между техобслуживаниями.
Задний мост ГАЗ-24 по конструкции принципиально не отличался от моста ГАЗ-21, сохраняя разъёмный картер из двух половин, стянутых болтами (так называемый мост типа Timken или Split). Это решение явно не относится к особо удачным, так как из-за меньшей точности установки шестерён при сборке такой мост получается пр прочих равных более шумным, чем мост с неразрезным картером, причём с большим потенциальным разбросом между отдельными экземплярами (хотя и намного менее шумным, чем любой мост без гипоидного зацепления шестерён, как на «Победе» или УАЗе), а также имеет меньшую жёсткость. Кроме того, для любого серьёзного ремонта, вроде замены главной пары, такой мост приходится снимать с машины и «половинить». Естественно, после кустарной переборки шумность, как правило, возрастала ещё больше, так как даже в те времена идеально выставить пятно контакта шестерён в таком мосту умели единичные количества мастеров (сегодня это и вовсе полузабытое ремесло).
Единственное преимущество такой конструкции моста помимо большей технологической простоты — это то, что при движении по картер в снегу или рыхлом грунте он создаёт меньшее сопротивление движению автомобиля, благодаря чему мосты с такими картерами всё ещё имеют определённое распространение на внедорожниках, но для легковушки это не столь актуально.
Стоит отметить, что разрезной мост встречался и на иномарках вплоть до 1980-х годов, например, его очень любила фирма «Пежо», причём в некоторых случаях в главной паре даже использовалась червячная (!) передача, другими производителями к тому времени давно считавшаяся устаревшей.
При всём при этом, старый «волговский» мост был очень надёжен и долговечен — вплоть до того, что главные пары от «Волги» зачастую ставили в мосты УАЗов, у которых этот узел как раз не отличался надёжностью, где они долго и успешно ходили даже с повышенными по сравнению с легковым автомобилем нагрузками. Автомобили с V8 имели штатный мост, за исключением передаточного числа главной пары, и никаких жалоб на его надёжность и долговечность также не возникало.
Главная пара заднего моста — с гипоидным зацеплением шестерён. «Чистая» «Волга» ГАЗ-24 имела главную пару с передаточным числом 4,1:1. На ГАЗ-3102 появилась главная пара с передаточным числом 3,9:1, соответствующая меньшему расходу топлива и несколько большим крейсерской и максимальной скорости автомобиля (что, однако, практически целиком компенсируется меньшим диаметром радиальных шин этих автомобилей). Тот же мост с парой 3,9 ставился и на ГАЗ-24-10. На автомобили с V8 в тот же мост ставилась главная пара с передаточным числом 3,38:1, ещё от «Волги» ГАЗ-23.
Только в середине девяностых годов на часть ГАЗ-3102 и ГАЗ-31029 стал в экспериментальном порядке устанавливаться задний мост с цельным неразрезным картером (типа Salisbury), который, несмотря на своё народное название, не имеет никакого отношения к «Чайке», за вычетом сходства самого используемого типа картера. Эти мосты тоже зачастую имели звуковое сопровождение при работе, порой более сильное, чем у прежних разрезных, но причиной тому было уже низкое качество обработки самих шестерён, имевших квалитет (степень точности) 8...9, а также нестабильное качество подбора их пар, осуществлявшегося «по старинке», на слух, и далеко не всегда достаточно тщательно.
Впрочем, со временем новый «волговский» мост всё же довели до ума — после 2006 года обработка шестерён его главной пары стала осуществляться на при помощи компьютеризированного комплекса оборудования немецких фирм Boehringer и Klingelnberg, что позволило на порядок повысить точность изготовления (квалитет 3...4) и полностью избавиться от посторонних шумов. Кроме того, было увеличено число зубьев на шестернях (при сохранении того же передаточного отношения), за счёт чего увеличилась площадь контакта и также снизился уровень шума. Прецизионная точность изготовления шестерён сделала возможным отказ от подбора их пар «по шумности» и от регулировочных шайб в узле, вместо которых была установлена конусная втулка, как на ГАЗели.
К сожалению, в качестве издержек внедрения новых, более современных и производительных технологических процессов, надёжность моста заметно снизилась — например, корпус дифференциала нового образца, подвергавшаяся процессу объёмной закалки, на многих машинах имел смехотворно малый ресурс. Конечно, со временем процент откровенного брака значительно снизился, однако, насколько мне известно, полностью изжить проблему так и не удалось до самого прекращения выпуска «Волги» осенью 2008 года.
Интересно, что в статье конструктора ГАЗа Н. А. Юшманова в журнале «Автомобильная промышленность» за август 1968 года сказано буквально следующее:
Устанавливаемый на первых партиях автомобилей задний мост, за исключением передаточного числа главной передачи, очень мало отличается от моста автомобиля ГАЗ-21, однако в дальнейшем он будет существенно изменен.
Вероятно, что переход на неразрезной картера моста, как на «Чайке», был запланирован уже тогда, но по каким-то причинам так и не состоялся.
Ходовая часть «Волги» — один из основных источников полярных мнений об автомобилях этого семейства.
В то время, как большинство производителей легковых автомобилей к тому времени уже перешли на бесшкорневую подвеску с шаровыми шарнирами, ГАЗ продолжал совершенствовать традиционную схему с резьбовыми втулками и шкворнями, и на то были свои причины.
Если на автомобиле появляется принципиально новая (вновь разработанная, не перешедшая с уже освоенной модели в порядке унификации) конструкция, отличающаяся от стандартной на данный момент или кажущаяся странно архаичной — в большинстве случаев это является следствием того, что конструкторы уже попробовали альтернативный вариант (путём испытания иностранных аналогов со схожими техническими решениями, либо собственных опытно-конструкторских работ), и выявили опытным путём, что в данном конкретном контексте он не работает.
Именно так было и со шкворневой подвеской — ещё в первой половине 50-х годов на ГАЗе были проведены пробеговые испытания иностранных автомобилей класса «Волги» с только появлявшейся тогда бесшкворневой подвеской, которые убедительно показали, что в имевшихся дорожных условиях она не работает — не имеет требуемых надёжности, живучести и ресурса, а следовательно — не может быть на данный момент успешно применена на автомобиле класса «Волги». Это не значит, что к данной схеме вообще не планировали обращаться, но очевидно, что при разработке «Волги» второго поколения проведённый конструкторами анализ показал, что переходить на бесшкворневую подвеску всё-таки пока ещё рановато.
Вторая причина появления конструкций, на первый взгляд не соответствующих своему времени — это специфические требования самих эксплуатантов (в случае «Волги» — в первую очередь таксомоторных парков), которые в гробу могли видеть те или иные технические решения, при всей их прогрессивности, ввиду банального недоверия, наличия собственных соображений или нежелания ломать годами сложившуюся систему обслуживания и ремонта автомобилей, «заточенную» под те или иные конструктивные решения.
С этой точки зрения крайне показательна история УАЗ-469, который начинали проектировать как прогрессивный заднемоторный вездеход с несущим кузовом и независимой торсионной подвеской всех колёс, но в итоге военные очень доходчиво и убедительно довели до сведения конструкторского коллектива завода, что им нужен просто улучшенный «козёл», с рамой и рессорно-мостовой ходовой.
Шкворневая независимая передняя подвеска на средину шестидесятых — начало семидесятых годов уже давно не выглядела технических новшеством, но и архаичностью никого не шокировала. Mercedes-Benz S-класса, легковой «Студебекер», «Фольксваген-Жук», целый ряд спортивных автомобилей (Triumph TR-6, Studebaker Avanti, MG, ...) и пикапов всё ещё использовали весьма схожие конструкции.
По сравнению с предыдущими моделями ГАЗ, эта подвеска была спроектирована полностью «с нуля» — от ГАЗ-21 и «Победы» была унаследована разве что только самая общая конструктивная схема (два рычага, стойка, шкворень, соединяющие их шарниры) — да и то претерпев множество изменений. Практически никаких общих деталей у этих подвесок нет.
Подвеска «Волги» ГАЗ-24 проектировалась на основе наработок по автомобилю большого класса — «Чайке» ГАЗ-13, достаточно сравнить их чертежи, чтобы увидеть большое сходство конструктивных решений, унифицированы и многие их детали.
Для исторической справки, первой независимой подвеской, разработанной на ГАЗ-е, была передняя подвеска «Победы» — и разработана она была после внимательного изучения агрегата довоенного немецкого Опеля «Капитен» (одна из наиболее распространённых моделей легковых автомобилей в послевоенном СССР). Ну, а на «Опеле» она в свою очередь представляла собой уменьшенное подобие подвески типа Knee-action автомобилей Cadillac и La Salle, выпускавшихся той же фирмой (General Motors) для американского рынка — между прочим, одной из первых в мире массовых независимых передних подвесок. Вообще же, сами по себе шкворни конструктивно восходят непосредственно ко временам конных экипажей.
Это независимая подвеска на двух кованых поперечных рычагах с витыми пружинами и торсионным стабилизатором поперечной устойчивости.
Цель, преследуемая разработчиками подвески, становится достаточно очевидна при первом же взгляде на неё: почти все её части отличаются просто таки необычайной массивностью и «чугунявостью». Например, балка подвески — кованый профиль толщиной примерно в руку (победовские и двадцать-первые штампованные балки оказались «недостаточно суровы» — со временем деформировались, из-за чего постоянно «уходил» развал колёс, причём на пожилой машине его регулировка часто уже не могла компенсировать возникший прогиб балки). Кованые рычаги также производят сильное впечатление, больше напоминая детали подвески грузовика или «джипа», чем легкового автомобиля.
В результате волговская подвеска вполне смиренно сносит такое обращение с собой, которое какие-нибудь «Жигули» или аналогичную европейскую малолитражку быстро отправило бы на помойку из-за необратимой деформации кузова в точках крепления подвески и, соответственно, невозможности выставить углы установки передних колёс (типичная проблема ВАЗов, постоянно эксплуатировавшихся в сельской местности, по грунтовке «с ветерком»; в том числе и по этой причине на селе частенько предпочитали «Москвич», не отличавшийся подобной тенденцией к самоуничтожению), с последующим образование трещин как на самих элементах подвески, так и на кузове, к которому она у них крепилась без полноценной поперечины.
Это, однако, совсем не означает, что владелец «Волги» может попросту «забить» на переднюю подвеску — скорее наоборот !.. Подвеска «Волги» конструктивно сложнее любой другой использовавшейся на массовых советских автомобилях и для своей успешной работы требует весьма регулярного и тщательного обслуживания. Без которого она — да, не разваливается совсем — но начинает люфтить, греметь, скрипеть и «жрать» резину (но при этом, что удивительно, зачастую сохраняет очень приличную плавность хода).
Проистекают отсюда, увы, и существенные недостатки — так, именно из-за массивности деталей, расположенных в районе ступиц колёс, шкворневая подвеска при прочих равных имеет ощутимо большую неподрессоренную массу, чем выполненная на шаровых шарнирах, а следовательно — на неровностях дороги машина в большей степени теряет управление из-за «подпрыгивания» передних колёс, в то время, как они должны в любой ситуации сохранять контакт с дорогой. Это не является принципиальной проблемой, вообще лишающей машину на шкворнях шанса на хорошую управляемость, но временами может оказаться вполне заметно при практическом вождении.
Однако, обо всём по порядку...
Передняя подвеска ГАЗ-24 представляет собой вполне самостоятельный агрегат, полностью подсобранный на своей поперечине, который при необходимости демонтируется с автомобиля в сборе. Соответственно, рычаги крепятся не к лонжеронами через хлипкие приваренные проушины, а непосредственно к балке; пружины и амортизаторы — тоже упираются в приливы на балке, никакого заигрывания с выносом их в пространство над верхним рычагом, при котором все толчки, возникающие при проезде неровностей дороги, передавались на сравнительно слабые брызговики моторного отсека. Вместе это гарантирует всей конструкции отменную живучесть и долговечность. Будучи один раз грамотно собрана с использованием кондиционных запчастей, волговская шкворневая подвеска при регулярном уходе может ходить очень долго. Даже если без обслуживания со временем она начинает скрипеть, люфтить, «жрать» резину — шансов полного выхода её из строя, тем более — разрушения чего либо, практически нет.
При этом создатели автомобиля уделили большое внимание упрощению обслуживания: в первую очередь, значительно уменьшилось число точек смазки даже по сравнению со многими бесшкворневыми аналогами тех лет (в основном за счет устранения масленок рулевой трапеции, которая получила герметичные шарниры, а также замены части стальных резьбовых втулок на резинометаллические шарниры, ко всему ещё и хорошо гасящие вибрации, возникающие при проезде неровностей дороги) и увеличился межсервисный интервал. Появилась возможность регулировки развала колёс специальными прокладками, а не эксцентриковыми резьбовыми втулками в головках стойки, были внедрены более долговечные роликовые подшипники шкворней и другие технические решения, выгодно отличающие её от предыдущих моделей.
Попробуем, что называется, «на пальцах» разобраться, как устроена подвеска «Волги» ГАЗ-24.
В ней четыре поперечных кованых рычага, которые задают движение каждого из колёс независимо от перемещение другого.
Внутренние концы рычагов прикреплены к балке подвески через резинометаллические шарниры. Их конструкцию мы рассмотрим на примере шарнира нижнего рычага — группа деталей 21—28 на чертеже, приведённом чуть выше.
Они представляют собой резиновую втулку 27, которая вместе со вставленной в её внутренний канал металлической распорной втулкой 25 запрессовывается с натягом в отверстие головки рычага подвески 28.
Когда крепёжный болт нижнего рычага 26 со специальной резьбой, предотвращающей самоотворачивание (или, в случае верхних рычагов, гайка 34) затягивается, он намертво зажимает распорную втулку шарнира между осью рычага с одной стороны и шайбой — с другой, не давая ей возможности проворачиваться на оси. При этом эта шайба 24 сдавливает резиновую втулку, так что она раздаётся и силой трения оказывается намертво связана и с распорной втулкой, и с поверхностью отверстия в головке рычага, внутрь которого она запрессована. Детали 21—23 служат для ещё более надёжного предотвращения самоотворачивания болта, так как от того, насколько туго он будет затянут, зависит вся работа узла: нет нужной степени затяжки — нет достаточного трения между компонентами шарнира — начинается проскальзывание, а значит — и быстрый износ.
Таким образом, вся подвижность резинометаллического шарнира обеспечивается исключительно за счёт скручивания резиновой муфты. Никакого взаимного проскальзывания частей при этом в исправном шарнире не происходит — а значит, нет и трения, нет и износа. Конечно, сама резиновая втулка от постоянного закручивания и раскручивания, а также естественного старения материала, со временем таки выходит из строя — рвётся — но качественного изделия хватает на много десятков тысяч километров пробега.
Иногда спрашивают, так чем же отличается резинометаллический шарнир от сайлент-блока ? Так вот, первый термин — просто более общий; сайлент-блок — это частная разновидность резинометаллического шарнира. В отличие от разборных резинометаллических шарниров ГАЗ-24, у него резиновая вставка на заводе намертво привулканизирована к двум трубчатым металлическим втулкам, из которых одна служит наружной, а вторая — распорной. Сайлент-блок просто запрессовывается в сборе в предназначенное для него отверстие. На сайлент-блоках собрана подвеска ГАЗ-31105 (шаровая).
Так как резина эластична, она, помимо выполнения своей основной функции — обеспечения вращения рычагов вокруг своих осей, также в определённой степени смягчает передаваемые подвеской на кузов толчки.
Резинометаллические шарниры не требуют смазки в процессе эксплуатации, так как в них отсутствует трение: вся подвижность обеспечивается за счёт эластичности резины. Если по какой-то причине в таком шарнире происходит взаимное прокручивание деталей, долго он не проживёт — необходима замена. По той же причине необходимо постоянно следить за тем, хорошо ли затянуты болты и гайки, прижимающие распорные втулки к осям.
Внешние концы рычагов, к которым крепятся колёса, соединены между собой стойкой, к которой непосредственно крепится шкворень — деталь 8 на чертеже. Здесь уже используются не резинометаллические, а резьбовые шарниры.
Принцип действия резьбового шарнира я попробую пояснить буквально на пальцах. Для этого достаточно взять в руки болт потолще с навинченной на него гайкой (которая достаточно свободно ходит по его резьбе). Так вот, в данном примере гайка будет внешней резьбовой втулкой, а болт — распорной втулкой. Болт зажмите за его концы между большим и указательным пальцем расположенной горизонтально правой руки — эта рука от локтевого сустава до кончиков пальцев будет нашим рычагом подвески.
Пальцами расположенной вертикально левой руки при этом удерживайте навёрнутую на резьбу болта гайку, — левая рука будет аналогом стойки. Теперь, продолжая удерживать гайку пальцами левой руки и не сдвигая локтевой сустав правой, поводите левой рукой вверх-вниз, имитируя движение стойки при проезде неровностей дорожного покрытия. Вы почувствуете, что при этом гайка свободно проворачивается относительно винта, идя по его резьбе и при этом немного смещаясь то вправо, то влево. Примерно так и работает резьбовой шарнир.
Распорная резьбовая втулка 19 зажата между головками рычага подвески при помощи проходящего внутри неё пальца с гайкой (детали 2 и 7 на предыдущем чертеже, где показаны рычаги подвески), удерживаясь от проворачивания нанесённой на её торцы и на ответные плоскости головок рычага насечки. Внешняя же резьбовая втулка 15 намертво запрессована в головку стойки 17/18. При работе подвески внешняя втулка проворачивается относительно распорной, при этом двигаясь по её резьбе — точно так же, как гайка, навинченная на болт, в нашем примере. Естественно, при этом она немного смещается влево или вправо относительно распорной втулки, так сказать накручиваясь на неё или наоборот откручиваясь, поэтому в конструкции предусмотрен боковой зазор, который уплотняется резиновыми колечками (на чертеже не показаны). Для смазки узла служит пресс-маслёнка 16.
Изначальным проектом ГАЗ-24 предусматривалось использование не требующих обслуживания резинометаллических шарниров как на внутренних, так и на наружных концах рычагов передней подвески. Однако испытания первых же прототипов автомобиля быстро выявили недостаточную долговечность резиновых шарниров при работе на наружных концах рычагов, вследствие чего уже к лету 1965 года они были заменены в этом месте на резьбовые втулки (при этом, посадочные места остались те же самые, и вместо «резинок» на осях рычагов спортсмены нередко ставят резьбовые втулки от стоек).
Стоит отметить, что резьбовые шарниры всё же имеют и одно неоспоримое преимущество: хорошо смазанные резьбовые втулки проворачиваются друг относительно друга с чрезвычайной лёгкостью, в то время, как в резинометаллическом шарнире всегда присутствует определённая упругая деформация резиновой вставки, за счёт чего жёсткость подвески увеличивается, а комфортабельность езды, напротив, падает, что особенно чувствительно при небольших ходах подвески во время проезда мелких неровностей, которые ощущаются водителем и пассажирами как постоянные слабые толчки. Наиболее заметно это становится при отрицательных температурах, когда вязкость резиновой смеси резко повышается, в то время, как смазанной подвеске на резьбовых втулках никакой мороз не страшен.
Во многом именно по этим соображениям до середины семидесятых годов в подвеске Mercedes-Benz S-класса (даже после его перехода на бесшкворневую подвеску) в креплениях рычагов на подрамнике использовались именно резьбовые втулки — в точности как у ГАЗ-21. При этом, как и конструкторы ГАЗ-а, немцы отказались от использовавшейся на более ранних моделях централизованной смазки, вернувшись к старым добрым пресс-маслёнкам и шприцу.
Кроме того, резьбовые шарниры также обеспечивают существенно меньшее изменение установочных параметров подвески под воздействием внешних сил по сравнению с резинометаллическими, которые всегда сохраняют некоторую податливость из-за эластичности резины. Практически все специально разработанные для чистого спорта подвески собираются именно на резьбовых втулках и специальных сферических шарнирах, потому что никакие резинометалличесие шарниры не смогут удержать геометрию подвески в жёстких рамках изначально заданных установок под воздействием характерных для автоспорта огромных нагрузок.
В более «гражданских» спортивных автомобилях эту излишнюю податливость резиновых элементов подвески стараются компенсировать, вводя в подвеску дополнительные рычаги и растяжки, что, естественно, дополнительно повышает сложность и стоимость подвески.
На автомобилях ЗИС в подвеске вместо нижних резьбовых втулок стойки использовались подшипники: два игольчатых радиальных и один упорный для воспринятия осевого усилия. Это сложное и дорогое решение, но, видимо, вносившее свой вклад в обеспечение высокой плавности хода. При этом в верхнем шарнире стойки, а также внутреннем шарнире поперечной части нижнего рычага, использовались резиновые втулки, а на заднем конце продольной части нижнего рычага — шаровой шарнир. В общем — едва ли не полная коллекция всех основных типов шарниров в отдельно взятой подвеске !
Теперь подходим непосредственно к шкворням.
Шкворень (13 на чертеже) — это по сути ось, вокруг которой при поворотах вращается несущий колесо и передний тормозной механизм поворотный кулак 16. Для установки шкворня на стойке подвески имеются крепления в виде приливов со сквозными вертикальными отверстиями. Поворотный кулак неподвижно закреплён на шкворне поперечным штифтом 12, входящим в одну из лысок а, и вращается с ним как единое целое.
Вертикальное перемещение шкворня ограничивает установленный между поворотным кулаком и верхним приливом стойки опорный шариковый подшипник 11 — именно на него приходится весь вес передка машины, когда её колёса находятся на земле, а также все вертикальные толчки, возникающие при проезде дорожных неровностей. Зазор в узле выбирается регулировочной шайбой 14.
Боковые усилия такой подшипник воспринимать не способен, поэтому наряду с ним используются роликовые подшипники шкворня 8 — по одному в каждом приливе стойки. Если они изнашиваются и шкворень начинает люфтить в боковом направлении — упорный шарикоподшипник тоже очень быстро разбивает. Снизу и сверху отверстия в приливах поворотного кулака для роликовых подшипников шкворня закрыты заглушками — так называемыми пятаками на сленге волговодов.
На ГАЗ-21 упорный подшипник шкворня был аналогичен, а вот вместо игольчатых подшипников использовались бронзовые втулки. Недостатком этого решения было то, что при замене шкворня запрессованные в поворотный кулак новые втулки приходилось долго и муторно разворачивать в необходимый размер, для чего требовались опыт и специальный инструмент (развёртка), и даже после этого шкворень «залезает» в них с большим усилием (запрессовывается или забивается, в зависимости от наличия оборудования и фантазии мастера).
Такое устройство данного узла было полностью унаследовано ГАЗелью (тот же самый диаметр шкворня — 25 мм, те же самые втулки), владельцам которой хорошо известны все страдания при ремонте данного узла.
Применённая на ГАЗ-24 конструкция намного более технологична в ремонте, в частности — не требует никаких подгонок деталей. Минусом же игольчатых подшипников шкворня является то, что для их смазки приходилось использовать жидкое масло, а не консистентную смазку, что менее удобно с эксплуатационной точки зрения — об этом также см. ниже.
Шкворень на стойке подвески размещён не строго вертикально, а с определёнными углами продольного и поперечного наклона для обеспечения необходимых установочных параметров подвески.
Недостаток такой конструкции напрямую проистекает из описанного выше её принципа действия.
Как и любое резьбовое соединение, для лёгкого скольжения частей друг относительно друга без износа резьбовой шарнир требует смазки, причём регулярной и довольно обильной. Всё бы хорошо, если бы её можно было заложить в него раз и навсегда, как в шаровой шарнир бесшкворневой подвески — но не тут-то было ! Из-за наличия в нём конструктивно обсусловленного зазора по бокам от внешней втулки, резьбовой шарнир не герметичен. А значит, смазка из него активно вымывается. Теоретически они конечно имеют уплотнения, но на практике полной герметичности они не обеспечивают, особенно в изношенном виде.
Стало быть, если в современные шаровые опоры смазка закладывается обычно на заводе и на весь срок службы, то волговские резьбовые шарниры нужно регулярно шприцевать через предусмотренные в них пресс-маслёнки под смазочный шприц, закладывая в них смазочный материал — который со временем окисляется, загрязняется, вымывается, и так далее.
Так же, как и резьбовые шарниры, роликовые подшипники шкворня требуют регулярной смазки. Верхний подшипник смазывается через собственную пресс-маслёнку, а вот нижний — через общую с нижней резьбовой втулкой, причём смазке для того, чтобы попасть к резьбовой, приходится сначала пройти через подшипник, а затем — через довольно длинный канал внутри стойки:
Это нередко становится причиной «непроходимости» именно нижней пресс-маслёнки (другая причина — близость к дороге, соответственно — к воде, грязи и пыли). Причём «пробивать» забитые каналы давлением смазки не рекомендуется — с высокой вероятностью выдавит нижнюю заглушку шкворня («пятак») и износ ускориться многократно… После этого спасает только переборка.
В старой литературе встречается рекомендация врезать с каждой стороны по отдельной пресс-маслёнке для смазки нижней резьбовой отдельно от подшипника шкворня. В реальности с подобными переделками я не встречался, но на форумах их описания встречал, видимо, свой эффект они давали.
Смазывать подвеску приходится относительно часто. Заводская инструкция рекомендовала шприцевать подвеску при каждой замене масла в двигателе — раз в 6...6,5 тыс. км. На практике это старались делать существенно чаще, особенно в сырую погоду. Причём консистентные смазочные материалы (густые смазки вроде солидола или литола, говоря обычным языком) в подвеске ГАЗ-24 по целому ряду причин использовать нельзя, хотя соблазн есть и большой.
Основная причина — недостаточные характеристики смазок тех лет (и массовых современных тоже) с точки зрения вязкости базового масла (а она должна быть высокой, так как нагрузки в данном узле большие) и химической стабильности. Из-за низкой стабильности смазка коксуется внутри смазываемого узла и от этого, во-первых, прекращается нормальное смазывание иголок самого подшипника, а во-вторых — забиваются каналы для смазки. В результате узел приходится перебирать.
Инструкция рекомендует использовать жидкие трансмиссионные масла — нигрол (ТэП-15), также используют ТаД-17 или любое другое трансмиссионное масло. При шприцевании они заодно промывают узел от загрязнений. Естественно, жидкое масло, особенно при плохом шприце, часто льётся не только в шарнир, но и орошает всё вокруг, включая осуществляющего смазывание.
Конечно, по сравнению с «джентельменским набором» полностью построенной на резьбовых втулках подвески и также требующих смазки рулевых тяг «Волги» ГАЗ-21 — 19 (!) пресс-маслёнок — на ГАЗ-24 их «всего ничего», шесть штук. Остальное — уже резинометаллические шарниры, а на рулевых тягах — шаровые шарниры с пластиковыми вставками или с «пожизненным» запасом смазки.
Впрочем, и регулярная шприцовка не спасает от износа — со временем из-за пренебрежения смазочными работами, эксплуатации по грязи, износа, окисления не полностью вымываемой из шарниров смазки, и так далее, каналы для прохода смазки всё-таки забиваются, и резьбовые втулки на пару со шкворнями оказываются на голодном масляном пайке, что незамедлительно сказывается на их самочувствии. Тогда спасает только переборка с прочисткой. В целом, ресурс волговской подвески между переборками составляет от 50 до 80...100 тыс. км — в зависимости от множества факторов, включающих условия эксплуатации, частоту смазывания, качество смазочных материалов и использованных при предыдущей переборке деталей, и так далее.
На ГАЗели Бизнес таки сделали герметизированные шкворневые узлы. От шприцевания это не избавило, но межсервисный интервал увеличился солидно — до уровня в своё время использовавшихся смазываемых через пресс-маслёнки шаровых шарниров.
Кстати, на автомобилях с централизованной смазкой шасси шарниры жили в два-три раза дольше, но от неё завод отказался ещё в 1960 году из-за низкой надёжности самой системы, в основном обусловленной отсутствием в стране подходящих сортов качественной маслостойкой резины, и целого ряда других факторов. Решение — спорное, но в какой-то мере вынужденное.
Как уже говорилось, выбор в пользу шкворней при проектировании автомобиля был вполне осознанным. Например, проектировавшийся одновременно с ГАЗ-21 и во многом теми же людьми «Москвич-402» получил шаровые шарниры в подвеске уже в 1956 году. Дело в том, что на тяжёлом автомобиле класса «Волги» живучесть бесшкворневой подвески при эксплуатации по плохим дорогам была с используемыми в те годы материалами невысока. Например, на испытывавшемся в своё время на заводе «Форде» модели 1954 года шаровые шарниры рассыпались после пробега около 50 тысяч километров по рядовым советским дорогам. Впрочем, примерно таков ресурс шаровых шарниров и в подвеске многих современных автомобилей.
Шкворни же более прочны и, кроме того, даже при износе не могут вызвать неисправности, угрожающей способности автомобиля самостоятельно передвигаться. Случаи, когда шкворни ломаются, настолько редки, что их можно скорее объяснить заводским браком конкретной детали (в основном это происходит от сильных ударов на скорости о бордюр или при ДТП, когда шкворень получает огромную поперечную нагрузку «на излом», на которую он, в общем-то, и не рассчитан: при проезде неровностей дороги шкворень нагружен в основном на сжатие через упорный подшипник, в повороте же нагрузка на него в боковом направлении намного меньше и не имеет ударного характера).
В общем — при проектировании новой модели конструкторы ГАЗ-а решили, что конструктивный потенциал шкворневой подвески всё ещё не исчерпан. Разумеется, никто при этом не думал, что эта модель продержится на конвейере до двухтысячных годов: вплоть до конца шестидесятых модельный ряд ГАЗ-а полностью обновлялся примерно раз в десять-пятнадцать лет, и завод имел полное основание полагать, что к началу восьмидесятых годов на смену 24-тому шасси уже будет идти полностью новая платформа.
К тому же, основным назначением «Волги» была работа в таксопарках и ведомственных гаражах, в условиях централизованного обслуживания и ремонта. И сравнительная трудоёмкость обслуживания и ремонта шкворневой подвески (её переборка существенно сложнее, чем шаровой, и требует множества специальных «приспособ») при этом была не так заметна за счёт наличия квалифицированных ремонтников и хорошо оборудованной ремонтной базы.
Что касается необходимости постоянного обслуживания, то его объём на ГАЗ-24 был существенно уменьшен по сравнению с предыдущей моделью и вполне сравним с таковым на аналогичных иностранных. Например, у полноразмерных автомобилей Ford и Mercury конца шестидесятых — начала семидесятых годов передняя подвеска имела 8 пресс-маслёнок, которые шприцевались каждые 6 месяцев или 6 000 миль (11 000 км). То есть, по объёму обслуживанию шкворневую подвеску «Волги» удалось вплотную подтянуть к современным ей бескворневым подвескам иностранных аналогов тех лет.
Более современные Ford Crown Victoria, Chevrolet Caprice Classic и всевозможные «траки» (большие пикапы и внедорожники) тоже шприцевались при каждой смене масла, то есть, каждые 5...10 тысяч километров, в зависимости от условий эксплуатации. Причём причины в сохранении пресс-маслёнок здесь, сдаётся, те же, что и у создателей «Волги» — например, Crown-Victoria с восьмидесятых-девяностых годов используются почти исключительно «копами» и таксопарками, — а это, опять же, централизованное техническое обслуживание. Как бы ни были долговечны шаровые шарниры с заложенным в них пожизненным запасом смазки, их ресурс может быть увеличен ещё больше за счёт периодического обслуживания, и если такая возможность экономически целесообразна — никто в здравом уме от неё не откажется.
На лёгких грузовиках японского производства (Toyota Dyno, Nissan Atlas, Isuzu Elf и т.д.) шприцуемые металлические резьбовые втулки в креплениях рычагов передней подвески применяются вместо резиновых сайлент-блоков до сих пор. Для них частое обслуживание также не является недостатком, тем более что современные смазочные материалы позволяют довести его периодичность до разумных сроков. Так что коммерческий транспорт зачастую делает выбор в пользу периодически обслуживаемых узлов подвески и наши дни.
Главный же враг такой подвески (как, впрочем, и любого другого агрегата «Волги») — запчасти с нестабильным качеством и халтурная переборка с нарушением регламента работ.
«Волгу» вообще в целом можно назвать «машиной регулировок», а её подвески это касается в особой степени. В ней мало просто «свинтить» детали вместе — надо ещё и всё правильно настроить, в частности — отрегулировать все зазоры, обеспечив нормальную длительную работу узла. В этом отношении ГАЗ-24 всё же более технологична, чем предыдущая модель — к примеру, нет нужды развёрткой, с соблюдением соосности, подгонять бронзовые втулки в нужный размер перед тем, как запрессовать в них шкворень, так как вместо них применены не требующие подгонки роликовые подшипники. Но и на ней для качественного ремонта ходовой части требуется немало сноровки и умения.
На современных машинах подвеска собирается из подсобранных на заводе готовых узлов — «модулей», полностью отрегулированных, смазанных и подготовленных к работе и требующих от сборщика только крутить болты (желательно, но не обязательно — с нужным моментом), что значительно снижает требования к квалификации обслуживающего персонала. Однако при этом теряется ремонтопригодность на уровне самих «модулей», значительно увеличивается стоимость запасных частей. В последние десятилетия данная тенденция доходит до маразма — для замены маленькой детальки приходится покупать весь узел в сборе, например, шаровую опору вместе с рычагом и сайлент-блоками, или ступичный подшипник в сборе со ступицей, а то и приводным шарниром равных угловых скоростей. «Волга» спроектирована на совершенно иных принципах — всё в ней разбирается «на атомы», но при сборке и в процессе эксплуатации требует квалифицированной настройки.
Не обоснованы и претензии к шкворням как таковым в плане управляемости. Вопреки имеющемуся мнению, управляемость автомобиля определяется преимущественно не конструкцией подвески — шкворневая она или нет — а её геометрией и кинематикой. Хорошее доказательство тому — Chevrolet Corvette пятидесятых-шестидесятых годов, Studebaker Avanti, различные британские спортивные модели, вроде MGB, и прочие спортивные автомобили с весьма хорошей управляемостью и, при этом, шкворневой подвеской. Подвеска типа HiPer strut, используемая на последних моделях Saab, Opel и Buick, по сути тоже является шкворневой, как и тойотовская SuperStrut. Да и на ГАЗ-3102 и ГАЗ-3110 те же самые в принципе шкворни ведут себя уже совсем по-другому благодаря иным установочным параметрам.
Что касается небольшого рыскания на скоростях за 120 км/ч, свойственного всем машинам 24-того семейства, то его причина хорошо известна — настройка передней подвески с нулевым кастером, углом продольного наклона шкворня (заводская инструкция рекомендует поддерживать его в пределах 0±1°). Данная настройка подвески являлась стандартной вплоть до появления повышенных требований к управляемости автомобилей на высокой скорости и соответствует минимальному усилию на рулевом колесе при менее чёткой реакции на движения рулём и достаточно вялом самовозврате «баранки» в среднее положение при прохождении поворота.
Такие же или близкие параметры предусматривала и заводская установка передней подвески американских автомобилей тех лет; например, для шасси Ford Falcon рекомендовалось поддерживать кастер в пределах от 0° до 1° (см. инструкцию). Для построенного на том же шасси Ford Granada (1975) этот параметр изменили, увеличив кастер до 2°, что тут же улучшило поведение машины на дороге. Часто для версии автомобиля с гидравлическим усилителем задавался большой кастер, а для варианта без него — поменьше, для снижении усилия на руле.
Данные по установочным углам подвески на некоторых других автомобилях американского рынка можно найти в таблице. Как видно, наибольший кастер задаётся для подвески спортивных моделей, наименьший — для рядовых семейных седанов. У переднеприводных машин может быть и довольно большой отрицательный кастер — для них эта настройка имеет совершенно иное значение, чем для заднеприводных.
На «Чайке» ГАЗ-13, более быстроходной по сравнению с «Волгой» и с завода оснащавшейся ГУРом, тоже был предусмотрен заметный положительный кастер (до 1º30').
В Европе этому параметру стали уделять внимание намного раньше, например, на Fiat 124 и, соответственно, «Жигулях» ВАЗ-2101, кастер составлял уже 3°30'±30'; на ВАЗ-2105/07 его увеличили до 4°. Кроме того, на более лёгкой машине повышение усилия на руле, вызванное такой настройкой подвески, было не так заметно.
В целом, однозначно удачного решения данной проблемы без «включения в формулу» усилителя рулевого управления попросту не существует. Так, на спорткаре Iso Rivolta (1962-70) передние колёса были установлены с кастером 7° 30', что обеспечивало великолепную курсовую устойчивость даже на 200 км/ч, однако платой за это стало очень тяжёлое рулевое управление с 5 оборотами между крайними положениями рулевого колеса...
То есть, здесь, как и во многих других элементах конструкции «Волги», имел место компромисс: разработчики получили лёгкий руль путём некоторого, приемлемого для тех задач, которые ставились перед проектируемым автомобилем, ухудшения устойчивости и управляемости на скорости.
Кстати, из этого вытекает категорическая недопустимость задирать «Волге» зад за счёт усиления задней подвески, так как вместе с кузовом при этом наклоняется вперёд и ось поворота передних колёс. У других автомобилей — даже у классических «Жигулей» — есть хотя бы минимальный запас положительного угла наклона оси поворота передних колёс, который можно сравнительно безболезненно «выбрать» при завышении задней подвески относительно передней: ну, был кастер небольшим положительным — станет нулевым, ухудшится управляемость, но на машине всё же можно будет ездить.
А вот у «Волги» такого запаса нет. И при задранной задней части у неё нулевой кастер очень быстро сменяется отрицательным. А это — уже неминуемая динамическая дестабилизация передних колёс при движении. Проблемы с курсовой устойчивостью — обеспечены. Не говоря уже о том, что при, например, отказе одного из колёсных тормозных цилиндров или обрыве рулевой тяги на скорости это — практически верная авария.
Между тем, со временем изменения в характере дорожного движения привели к существенному росту фактических скоростей, и требования к управляемости автомобилей стали существенно жестче, что потребовало пересмотра приоритетов в этой области. Когда во второй половине семидесятых годов проектировалась модернизированная «Волга» ГАЗ-3102, конструкторы учли этот факт, увеличив конструктивный (обеспеченный конструкцией стойки подвески и поворотного кулака) угол продольного наклона шкворня до +6°. Это сразу же решило проблему рыскания: «ноль-вторая» вполне комфортно чувствовала себя на любых доступных ей скоростях и в целом управлялась намного лучше, но при этом рулевое колесо стало существенно более тугим.
На ГАЗ-3110 эта установка шасси была сохранена, а проблема слишком тугого руля была со временем решена введением гидроусилителя. Таким образом, ГАЗ сумел «выжать» из шкворней всё, что только было возможно. Пожалуй, единственными нерешёнными проблемами управляемости в волговской шкворневой подвеске самого позднего образца остались невыгодное изменение развала передних колёс при ходе сжатия, несколько уменьшавшее предельную скорость автомобиля в повороте, и отсутствие так называемой «противоклевковой» геометрии, уменьшающей «приседание» передка автомобиля при торможении — увы, но ни то, ни то принципиально недостижимо при сохранении шкворней. Положительное их решение оказалось возможным лишь на «шаровой» подвеске ГАЗ-31105.
У моделей же с барабанными тормозами (24-10, 31029) осталась старая, «двадцать-четвёртая» настройка подвески, вполне соответствующая безопасным для автомобиля с такой тормозной системой скоростям.
К сожалению, решить проблему регулировкой вряд ли получится — её пределы для данного параметра у подвески ГАЗ-24 крайне невелики (не более 15 прокладок под осями верхних рычагов с каждой стороны подвески) и годятся лишь для устранения последствий износа или нарушения геометрии. К тому же, с продольным наклоном шкворня жёстко связан другой параметр — поперечный наклон, регулировать их надо вместе, а такой возможности подвеска ГАЗ-24 не предоставляет.
Интересно, что в подвеске ГАЗ-21 поперечный наклон шкворня таки регулировался в некоторых пределах за счёт эксцентрических резьбовых втулок в головках стоек — в этой подвеске таким образом устанавливались и развал, и продольный с поперечным наклоны шкворня; конструкция достаточно остроумная, но сильно затрудняющая регулировку — проворачивая эксцентриковые втулки «поймать» нужный момент, когда все параметры подвески одновременно находятся в поле допусков, задача обычно весьма нетривиальная.
Да и заводская инструкция недаром предписывала именно такие настройки — увеличение кастера при сохранении остальных параметров неминуемо повлечёт за собой увеличение усилия на рулевом колесе и очень резкий самовозврат.
Замечу, что по состоянию на 2007 год на гоночных машинах заводской команды ГАЗ стояли именно шкворневые подвески, причём от ГАЗ-3102 раннего образца (у неё была самая большая в семействе колея — 1510 мм), с 14-дюймовыми колёсами на 5 шпильках. Разумеется, с полностью изменёнными настройками и кучей кастомных деталей. У команды Лукойла — насколько мне известно, тоже.
Другое дело — что и сама по себе настройка подвески в целом у ГАЗ-24 была «американская», ориентированная на комфорт, а не управляемость. Впрочем, по сравнению со многими американскими полноразмерными седанами шестидесятых и первой половины семидесятых годов управлялась «Волга» всё же довольно неплохо — имела адекватные крены в поворотах, меньше «приседала» при разгоне и «клевала» при торможении, меньше галопировала при проезде препятствий, имела довольно острую реакцию на руль: сказывалась «сверхмягкая» подвеска американских «крейсеров» (см. картинку), их физически больше размеры, а следовательно — масса и инерция агрегатов шасси, менее жёсткие рамные кузова (волговский цельносварной несущий кузов был жёстче по сравнению и с рамными, и со многими американскими автомобилями с несущим кузовом и отдельным подрамником, крепящимся через толстые резиновые подушки), а также характерный для многих из них перегруженный из-за тяжёлых двигателей перед (в то время, как у «Волги» с её лёгким алюминиевым двигателем развесовка была близка к идеальной: 53% массы приходилось на переднюю ось, 47% на заднюю).
Ещё одна проблема подвески «Волги», общая для многих автомобилей выпуска 1930-х — 60-х годов с независимой передней подвеской — это её неудачная с точки зрения управляемости кинематика. В те годы шины были диагональными и изнашивались по современным меркам очень быстро, и в особенности быстро — если при работе подвески заметно менялась колея и развал. Поэтому основной задачей разработчиков было обеспечить минимальное изменение этих параметров при вертикальных ходах подвески с целью обеспечения ходимости шин. Влиянию характера изменения этих параметров на устойчивость и управляемость автомобиля много внимания ещё не уделяли.
«Дубль» ГАЗ-24-24, при всей схожести своего шасси со штатным двадцать-четвёртым, имел несколько иную управляемость: лучше держался на прямой на высоких скоростях, без характерного для «Волги» рыскания после 120 км/ч, более собранно проходил повороты благодаря усиленному стабилизатору поперечной устойчивости.
В задней подвеске использовались архаичные, но зато неубиваемые и идеально подходящие для создания грузовых модификаций рессоры с поставленными «под 45 градусов» амортизаторами. У машин первых лет выпуска рессоры были с прямоугольным профилем листов, шестилистовые, а на универсалах — семилистовые. С конца 1974 года их заменили пяти- и шестилистовыми соответственно с листами параболического профиля.
По сравнению с ГАЗ-21, рессоры стали длиннее, шире и с меньшим количеством листов, что способствовало улучшению плавности хода и управляемости. Появились толстые противоскрипные прокладки из полиэтилена, которые сделали работу рессор бесшумной и избавили от их постоянного смазывания графитной смазкой. Кроме того, мост сместили вперёд относительно середины рессоры на 95 мм, благодаря чему передняя часть рессоры, воспринимающая возникающие при движении автомобиля нагрузки и передающая их на кузов (по сути она играет роль рычага подвески), стала жёстче, геометрия подвески — стабильнее, а условия работы заднего карданного шарнира оказались более комфортными.
На начало семидесятых это всё ещё был один из наиболее распространённых типов подвески, особенно в американском автопроме. Даже в Европе, где на люкcовых седанах класса «Волги» уже в шестидесятых годах стала более-менее привычна независимая задняя подвеска, на менее претенциозных автомобилях рессоры продержались до конца семидесятых — начала восьмидесятых. Последним примером использования их на западноевропейском легковом автомобиле считается Ford Capri, который выпускался до 1987 года.
В Штатах General Motors и Ford к середине шестидесятых годов в основном перешли на пружины «по кругу», кроме бюджетных моделей; а вот Chrysler — что называется, до конца держался за рессоры в задней подвеске — где-то до середины восьмидесятых годов. Причём даже на очень дорогих моделях, для которых вопросы цены и технологичности играли совершенно второстепенную роль.
Почему ? Специалисты фирмы утверждали, что преимущество рессор в том, что они крепятся к кузову в двух точках, в отличие от пружин, которые упираются в него лишь в одной и поэтому сильнее передают на него толчки, которые рессоры более эффективно гасят, распределяя между двумя широко разнесёнными креплениями. Это позволяет также заметно облегчить конструкцию силовых элементов задней части кузова.
Кроме того, многолистовая рессора в определённой степени обладает свойством приспосабливаться к конкретным дорожным условиям: небольшие толчки воспринимаются более длинными и мягкими листами, а при проезде крупных неровностей покрытия включаются в работу более жёсткие короткие листы. В наибольшей степени таким свойством обладает рессора с отдельным подрессорником, выделенным из основного пакета.
Более того, внутрилистовое трение в рессоре является своего рода примитивным фрикционным амортизатором, что также добавляет езде комфортабельности (первые автомобили вообще не имели амортизаторов, толчки гасились только внутренним трением рессор).
К сожалению, внутреннее трение является также и серьёзным недостатком рессоры: трение означает износ. Со временем контактирующие друг с другом листы истирают друг друга, и рессора выходит из строя. Не помогают ни смазка, ни чехлы, ни прокладки между листами из антифрикционного материала. Единственный более-менее действенный вариант борьбы с износом рессор — так называемые «щелевые» рессоры, в которых листы практически не контактируют друг с другом и работают по сути как несколько объединённых друг с другом отдельных рессор, благодаря чему внутреннее трение практически отсутствует. Практически «вечны» и однолистовые рессоры с заменяющим весь пакет единственным листом, имеющим переменный профиль (но ценой значительного снижения надёжности — единственный лист такой рессоры ничто не страхует на случай его разрушения).
Главный же минус рессорной подвески — то, что податливые, эластичные рессоры под нагрузкой, возникающей при разгоне, торможении и в поворотах изгибаются «как хотят», вызывая пусть небольшое, но существенное для управляемости на высоких скоростях движения смещение заднего моста: геометрия подвески «гуляет», задний мост начинает «подруливать» в сторону, и поведение автомобиля становится практически непредсказуемым. У зависимой пружинной подвески же движение моста жёстко задаётся рычагами, причём чем их больше — тем точнее и, в целом, лучше. Исправить этот недостаток введением дополнительных реактивных тяг можно, но для серийного производства экономически нецелесообразно — проще перейти на рычаги и пружины
Ещё один недостаток — компоновочный: имеющие большую длину по соображениям обеспечения комфорта рессоры не дают уменьшить длину заднего свеса кузова, которая жёстко задаётся расположением их задних кронштейнов — а следовательно за задним мостом остаётся длинный «хвост», неудобный при маневрировании; большой получается и общая длина автомобиля, при сравнительно короткой колёсной базе. Это стало особенно ощутимо в семидесятых — восьмидесятых годах, когда из-за транспортной загруженности городов встал вопрос о более рациональной компоновке автомобилей, позволяющей уменьшить их габаритные размеры при той же вместимости салона. Использование пружинной подвески, в особенности независимой, позволяло заметно укоротить автомобиль, применив кузов «клиновидного» профиля с высоким и сравнительно коротким багажным отсеком, при сохранении полезного объёма последнего. Хотя мода на «хвостатые» автомобили ещё продержалась какое-то время на моделях среднего и большого литража, особенно в США, к середине восьмидесятых все легковушки новой разработки уже имели довольно короткий задний свес.
Подробнее о различных конструкциях подвесок можно почитать в технической статье.
Рулевой механизм ГАЗ-24 — типа «глобоидальный червяк — трехгребневой ролик», с задней рулевой трапецией. Для тех лет это был основной тип рулевого механизма, реечная система до середины семидесятых встречалась в основном на спорткарах.
На американских машинах, правда, любили ставить рулевое управление типа винт — шариковая гайка (recirculating balls), с передачей усилия от червяка к сектору или гайке через перекатывающиеся между ними металлические шары — так меньше усилие на руле. Этот механизм и сегодня можно найти на американских джипах, или, например, спортивном Chrysler Crossfire. А вот в Европе такое встречалось лишь на самых дорогих моделях легковушек или на грузовиках — в частности, на советском ЗИЛ-130, а также, из недавнего, на ГАЗели. На «Волгах» самых новых выпусков с ГУР тоже стояло рулевое управление с шариковой гайкой.
Рулевое управление ГАЗ-24 было спроектировано в расчёте на минимизацию усилия на рулевом колесе, для чего его передаточное число было увеличено до 19:1, почти как у грузовиков. В результате, в полном соответствии с «золотым правилом механики», число оборотов руля между крайними положениями составило аж четыре с половиной полных оборота, но усилия на рулевом колесе остались вменяемыми.
Не рекорд, конечно — на американских машинах без ГУР могло быть и 5-6 оборотов; а (анти)рекорд в размерном классе «Волги», видимо, принадлежит фирме AMC — 6,25 оборотов (!) на моделях Matador и Gremlin в варианте без ГУР; европейский Ford Zephyr Mk IV в позднем варианте имел 6,4 оборота между крайними положениями, также пав жертвой экономии производителя на гидроусилителе рулевого управления.
Вообще, в конце шестидесятых, когда ГУР в Европе ещё оставался достаточно экзотической опцией, а более плотный трафик в городах уже требовал более лёгкого и отзывчивого рулевого управления, снижение усилий на руле за счёт увеличения числа его оборотов было весьма актуальным техническим решением — даже на «малолитражках» число полных оборотов руля между крайними положениями редко было менее 4.
Для ГАЗ-3102, в меньшей степени ГАЗ-24-10, и всех более поздних моделей «Волги» без ГУР-а, с их более широкими колёсами, уменьшенного диаметра рулевым колесом и переработанной геометрией передней подвески, стало характерно крайне неблагоприятное сочетание довольно «тяжёлого» руля и большого числа оборотов между крайними его положениями. Это отнюдь не добавляет удобства управлению машиной на парковке, да и манёвр перестроения между полосами на малой скорости, например — при объезде автобуса, подъехавшего к остановке, также весьма значительно затрудняет и замедляет. Однако при плотности движения советских городов семидесятых-восьмидесятых годов это, видимо, не было большой проблемой.
Благодаря большим углам поворота передних колёс, по маневренности «Волга» почти не уступает «классическим» жигулям, что является очень хорошим показателем для машины этого класса (радиусы поворота у ГАЗ-24 и ВАЗ-ов одинаковы, при этом длина различается на 700 мм, база — на 380 мм). К тому же передний свес очень короток и позволяет вплотную «притираться» к бордюру при развороте в узких местах, чего не могут позволить себе владельцы более поздних «Волг», тем паче — последних моделей с низкими пластиковыми бамперами.
Кроме того, по сравнению с ГАЗ-21 перенос редуктора рулевого механизма за балку подвески, конечно же, значительно улучшил пассивную безопасность, так как при лобовом столкновении расположенный далеко впереди перед балкой подвески редуктор оказывается в деформируемой зоне и начинает двигаться назад, толкая всю рулевую колонку и руль в грудь водителя. С редуктором, защищённым мощной поперечиной подвески, шансы такого развития событий намного ниже.
Также где-то между 1972 и 1974 годами (более точного указания я пока не нашёл) в целях безопасности в рулевой колонке ГАЗ-24 появилась эластичная резиновая муфта, соединяющая рулевой вал с рулевым механизмом. При сильном ударе он рвалась, разрывая жёсткую связь между рулевым механизмом и рулевой колонкой, и тем самым предотвращая её «катапультирование» в водителя. По моему скромному мнению, такая система эффективнее, чем, скажем, применявшаяся на «Москвичах» и «Жигулях» телескопирующая рулевая колонка, которая при ударе не разделялась на две части, а просто складывалась от удара, уменьшая свою длину за счёт сминаемого сильфона посередине. Но, конечно, она уступает по безопасности современному рулевому управлению с «карданчиками».
Ключевая проблема этого рулевого механизма, как и всех ему подобных — люфты. Здесь свой вклад вносит и сам по себе червячный механизм, — со временем износ в нём достигает таких пределов, что регулировать его становится просто «некуда», соответственно, встречаются экземпляры с просто-таки криминальными люфтами в 20-30° — и обилие тяг и шарниров по сравнению с реечной системой, что также не добавляет рулевому управлению точности, особенно в изношенном состоянии. С другой стороны — именно длинные тяги рулевой трапеции и вечно немного люфтящие шарниры на них уменьшают передачу на руль ударов при проезде дорожных неровностей, да и сама по себе рулевая трапеций в сравнении с рейкой будет покрепче.
Шарниры рулевых тяг «Волги» отличаются от других современных ей автомобилей — они сохраняют «древнюю» конструкцию, которая использовалась как минимум ещё на ЗИМ-е ГАЗ-12, с закалённой металлической полусферой рулевого пальца, контактирующей со сферической ответной поверхность на металлическом корпусе шарнира. В более современных шарнирах как правило используются пластиковые вкладыши. Отсюда проистекают как преимущества, так и недостатки: в отличие от «одноразовых» современных шарниров, которые при появлении износа можно только заменить новыми, волговские служат многие годы без замены, но для этого требуется их пусть и не частое, но довольно трудоёмкое обслуживание.
Волговские шарниры рулевых тяг герметизированы резиновым пыльником и в процессе эксплуатации не требуют регулярной смазки, поэтому на них и нет пресс-маслёнок (в отличие от ГАЗ-21, где они имели лишь штампованные металлические щитки и не были герметичны, из-за чего их приходилось шприцевать с незавидной регулярностью для обновления смазки и удаления воды и грязи).
Руководство по эксплуатации рекомендовало даже при целом пыльнике менять смазку в шарнирах трапеции (с разборкой) раз в 60...80 тыс. км при эксплуатации на асфальтовых дорогах и вдвое чаще — на грунтовых, или же не реже, чем раз в два года. Также перебирать шарнир с заменой смазки требуется при потере пыльником герметичности. Смазка — марки ВНИИ НП-242 с дисульфидом молибдена, применение смазок без антифрикционных добавок (например, того же Литола) ведёт к снижению срока службы узла.
Некоторые владельцы самостоятельно врезали в шарниры пресс-маслёнки в надежде увеличить ресурс за счёт периодического шприцевания, что, как правило, заканчивалось порванным давлением смазки пыльником и сокращением срока службы шарнира. Пресс-маслёнка этим шарнирам нужна как рыбе зонтик, а нужны — герметичный пыльник и хорошая смазка с большим сроком службы без досмазывания.
Периодической регулировки шарниры рулевых тяг также не требуют, так как являются самоподтягивающимися — нормальный износ шаровой поверхности шарнира компенсируется за счёт мощной пружины, прижимающей палец к корпусу. Тем не менее, в процессе эксплуатации может понадобиться подтяжка нижней пробки шарнира для устранения зазора (люфта), если он всё же возник — о его появлении обычно говорят стук и пятнистый износ шин. Регулировка зазора в шарнирах рулевых тяг также требуется при их сборке-разборке, например для добавления или замены смазки.
В отличие от этого, у шарниров с пластиковым вкладышем появление заметного люфта говорит о предельном износе, после чего их можно только выкинуть (на некоторых старых автомобилях, вроде «Москвича», при хорошем состоянии пальца можно было также заменить сам вкладыш, который делался в виде двух половин; на более современных автомобилях, начиная уже с «Жигулей», шаровой палец залит в пластик и замене его вкладыш не подлежит).
Срок службы шарнира рулевой трапеции «Волги» составлял по заводским данным порядка 100 тыс. км до появления заметного износа (до первой подтяжки) при условии целого и герметичного резинового пыльника, а до предельного износа, уже не компенсируемого подтяжкой — до 150...200 тыс. км. Браковочный показатель — углубление пальца относительно плоскости нижнего торца шарнира более, чем на 16 мм.
На восьмицилиндровые «дубли» ГАЗ-24-24 и 24-34 устанавливался гидравлический усилитель рулевого управления с отдельным от рулевого механизма силовым цилиндром, по конструкции аналогичный «Чайке» ГАЗ-13 и в целом похожий на американские ГУРы шестидесятых годов (например, очень похожий агрегат стоял на Chevrolet модели 1960-64 годов). Сам рулевой механизм, судя по всему, стандартный (во всяком случае, в руководствах приводится передаточное число стандартного рудуктора — 19,1:1; есть неофициальная информация, что мог использоваться и редуктор с ПЧ 18,2:1).
Также очень похожая (но всё же отличающаяся) конструкция устанавливалась в полуэкспериментальном порядке и на отдельные экземпляры ГАЗ-3102 и ГАЗ-31029 (на иллюстрациях выше), пока в конце девяностых годов на ГАЗ-3110 не появился полностью новый ГУР, встроенный непосредственно в рулевой механизм.
Некоторые подробности относительно различных вариантов ГУРов для «Волги» также можно найти в данном посте и в этой теме в целом.
Усилитель состоит из трёх отдельных частей — насоса, золотникового устройства и силового цилиндра, связанных друг с другом резиновыми шлангами высокого давления.
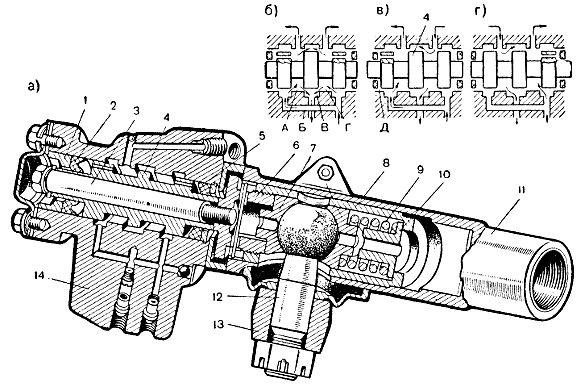
Здесь показан распределитель ГУР'а ГАЗ-66, но за исключением размера он по сути аналогичен использовавшемуся на легковых автомобилях. Сама конструкция, судя по всему, происходит от использовавшейся на автомобилях General Motors, в частности Chevrolet Corvette (конструктивное сходство очень сильное, хотя и видно, что технологическое оформление у отечественного изделия полностью своё).
Золотниковое устройство (распределитель) установлено на конце центрального звена рулевой трапеции, между самим звеном и сошкой на валу рулевого механизма. Золотник управляет потоком жидкости от насоса, причём он не является дозирующим устройством, а просто имеет три фиксированных положения — «включено влево», «включено вправо» и нейтральное. Его полости А и Г (см. схему) соединены с силовым цилиндром, полость Б — через нагнетающую магистраль с насосом, а полость В — через сливную магистраль с бачком.
Когда руль неподвижен, золотник пружиной приводится в нейтральное положение и через сливной маслопровод гоняет гидрожидкость по кругу между бачком и насосом (Б через А и Г соединено с В), при этом давление в обеих полостях гидроцилиндра одинаково и его шток остаётся неподвижным.
Но стоит водителю с достаточным усилием сдвинуть с места обод «баранки» — как золотник, следуя за сошкой рулевого механизма, преодолевая усилие пружины, смещается в сторону примерно на 1,5 мм и включает усилитель в работу, разобщая нагнетательную магистраль со сливной и одновременно соединяя нагнетательную магистраль с одной из полостей силового цилиндра, в зависимости от того, в каком направлении вращается руль. При этом через одну из выходных полостей распределителя (А или Г, в зависимости от направления поворота руля) масло под давлением нагнетается в соответствующую полость двустороннего силового цилиндра, оказывая давление на его поршень, связанный с центральной тягой рулевой трапеции, что снимает значительную часть усилия, требуемого для поворота рулевого колеса. Вторая выходная полость распределителя при этом соединяет противоположную полость силового цилиндра со сливной магистралью, так что масло из противоположной полости силового цилиндра выдавливается обратно в распределитель и далее в сливную магистраль.
Таким образом обеспечивается гидравлическое серводействие, значительно снижающее усилие на руле. Не убирающее его практически полностью, как у некоторых коаксиальных (встроенных в рулевой редуктор) ГУРов — руль не вращается «одним пальцем» и для того, чтобы в работу вступила гидравлика, к нему нужно приложить не чрезмерное, но вполне заметное усилие (порядка нескольких килограмм). Так что, столкнувшись с таким усилителем впервые, вы поначалу можете даже не понять, работает ли он или нет. Но поверьте — без него было бы ещё хуже.
Система рассчитана таким образом, чтобы одного только создаваемого давлением жидкости в силовом цилиндре усилия не хватало для поворота колёс — рулевая трапеция приводится в движение совместным действием давления гидрожидкости в силовом цилиндре и усилия, прилагаемого водителем к рулевому колесу и передающегося на трапецию через сошку рулевого редуктора. Давление жидкости компенсирует большую часть возникающего в рулевом приводе сопротивления повороту колёс, но даже при включенном ГУРе водителю остаётся «закончить» начатую им работу, преодолев оставшееся незначительное сопротивление, после чего колёса начинают поворачивать.
После того, как водитель прекращает поворачивать рулевое колесо, ГУР «самовыключается» за счёт того, что при неподвижном золотнике (связанном с неподвижной в данный момент сошкой на рулевом механизме) центральная рулевая тяга какое-то время продолжает двигаться в ту же сторону под действием давления в силовом цилиндре и почти сразу переводит золотник в нейтральное положение, перекрывая поступление жидкости в силовой цилиндр, после чего резко возрастающее сопротивление сразу же останавливает рулевой привод в текущем положении.
Обращаю особое внимание, что распределитель усилителя приводится в действие именно поворотом сошки рулевого редуктора, которое может происходить исключительно за счёт управляющего воздействия водителя — в то время, как силовой цилиндр воздействует непосредственно на саму рулевую трапецию. Это позволяет исключить самопроизвольное «убегание» руля от водителя, за счёт того, что сам по себе силовой цилиндр не способен привести золотник в рабочее положение — наоборот, он его выключает.
Агрегат вполне работоспособен, как и в случае аналогичных ГУРов старых «американцев» конструкторы даже попытались обеспечить некое подобие «обратной связи» — то есть, вы не будете чувствовать эффекта «вывешенных колёс». Однако ощущения от его работы всё равно весьма специфические. Самовозврат рулевого колеса в нейтральное положение всё же присутствует, но вяловат (как, в принципе, и у «Волги» без усилителя руля). Звуковое сопровождение при работе присутствует, но в пределах адекватного (гудит он, пожалуй, поменьше, чем борисовский ГУР на ГАЗ-3110 / 105), а вот подтекание гидравлической жидкости из многочисленных соединений трубопроводов и уплотнений может быть существенной проблемой на изношенной машине (точнее говоря — как минимум все золотники потеют маслом с новья, и сделать с этим практически ничего нельзя, и даже американские детали страдают тем же самым). Дополнительным бонусом от наличия ГУРа является практически полное отсутствие нагрузки на рулевой механизм, за счёт чего он практически не изнашивается.
В настоящее время это большой раритет, так что поддерживать его в работоспособном состоянии становится всё труднее, а уж на установку его на обычную «Волгу» в целях модернизации и вовсе не стоит рассчитывать — лучше при этом смотреть в сторону рулевого управления с ГУР нового образца (ГАЗ-3110, -31105). Он ещё и обеспечивает намного более острый руль (~2,5 оборота между крайними положениями), что предпочтительно для современных условий движения.
Тормоза ГАЗ-24 представляли собой шаг вперед по сравнению с ГАЗ-21, но не очень далекий.

1 — ГВУТ; 2 — задний левый колесный цилиндр; 3 — шланг к заднему мосту; 4 — педаль тормоза; 5 — ГТЦ; 6 — левые передние колесные цилиндры;
Тормоза по-прежнему барабанные на всех колесах, что было нормально для середины шестидесятых, когда машина проектировалась, но для Европы семидесятых уже видится явно устаревшим решением. В Штатах же дисковые тормоза на бюджетных автомобилях продолжали оставаться сравнительно редкой опцией вплоть до второй половины того же десятилетия.
Стоит отметить, что дисковые тормозные механизмы, вообще говоря, не являются заведомо более мощными, чем барабанные. При необходимости и дисковый, и барабанный тормозной механизмы могут быть спроектированы с любой необходимой мощностью в абсолютных величинах, хотя барабанный при этом и будет более громоздким (замечание для любителей школьной физики, не знающих ничего за её пределами: только не нужно путать мощность с тормозным усилием, которое от площади колодок не зависит — это совершенно разные вещи).
Однако, у дисковых тормозов имеются неоспоримые преимущества, проистекающие из самого их принципа действия — прижимания плоской тормозной колодки к плоской же поверхности тормозного диска. Стабильный и равномерный контакт двух плоских деталей друг с другом обеспечить намного проще, чем полукруглой колодки и цилиндрической поверхности барабана. Благодаря этому дисковые тормоза намного быстрее срабатывают и обладают постоянством характеристик на протяжении всего срока службы колодок, а также обеспечивают недостижимую для «барабанов» равномерность тормозных сил на одной оси. Сами колодки для них также проще и дешевле в производстве.
Отсутствует и необходимость регулировки в процессе эксплуатации (ручной или автоматической), так как нужный минимальный зазор между колодкой и диском в дисковом тормозе поддерживается конструктивно: в нём нет возвратной пружины колодок, благодаря чему они не отводятся от тормозного диска после торможения, как в барабанном тормозе, а всегда остаются в готовом к действию положению, и даже если колодка при этом слегка задевает за диск — ничего страшного в этом нет (иногда применяются очень слабые пружины, которые не способны задвинуть поршень гидроцилиндра суппорта обратно и нужны только для того, чтобы не давать колодкам плотно прижиматься к поверхности диска, что позволяет устранить их шелест при движении автомобиля, а также отчасти предотвращает их дребезжание на неровностях).
Если же в барабанном тормозе принудительно не отвести колодку от барабана после окончания торможения — то из-за свойственного барабанным тормозам эффекта «самоусиления» задевающая за барабан колодка будет увлекаться его вращением и прижиматься к нему всё сильнее, из-за чего это колесо будет самопроизвольно притормаживать на ходу. Это снижает усилие на педали при торможении, но из этого также проистекает необходимость после каждого торможения принудительно возвращать колодки барабанного тормоза в исходное положение, что и порождает проблему регулировки зазора между колодкой и барабаном. Дисковый тормоз от этого эффекта полностью свободен — сила, прижимающая колодку к диску, в нём зависит только от давления в гидросистеме, так как диск вращается в перпендикулярной направлению движения колодок плоскости и не увлекает их за собой.
В целом, барабанные тормоза адекватно справляются с задачей быстрой и безопасной остановки автомобиля со скоростей порядка 100 км/ч и менее при отсутствии затяжных торможений, приводящих к их перегреву и потери эффективности, а в особенности хорошо показывают себя в тяжёлых дорожных условиях, в которых играет положительную роль лучшая защищённость тормозного барабана от пыли и воды. Но при движении преимущественно по хорошим дорогам на высоких скоростях, особенно с резкими или затяжными торможениями, становятся предпочтительны дисковые тормоза с их постоянством характеристик, быстротой и равномерностью срабатывания, намного лучшим охлаждением и меньшей склонностью к перегреву благодаря хорошему рассеиванию тепла.
Не случайно в Италии, где многие дороги представляют собой горные серпантины, предъявляющие очень высокие требования к способности тормозов сохранять эффективность при длительном торможении, на дисковые тормоза быстро перешли даже производители бюджетных автомобилей вроде «Фиата». В СССР же в те годы оказалось более рационально поставить сзади «барабаны», ресурс колодок которых в условиях пыльных сельских дорог был в разы больше.
Именно поэтому на быстроходных легковых автомобилях давно уже перешли на «диски», а вот на сравнительно медлительных грузовиках и автобусах, где требуется большое тормозное усилие именно в абсолютном выражении, до сих пор часто используются «барабаны» (хотя на быстроходных дорожных грузовиках «диски» постепенно стали появляться ещё с конца 1980-х годов).
Колёсные тормозные механизмы ГАЗ-24 были в целом аналогичны ГАЗ-21: те же 11-дюймовые барабанные тормоза с двумя гидроцилиндрами спереди (дуплексные) и одним цилиндром, воздействующим сразу на обе колодки, сзади. Однако существенным нововведением были «самоподводящиеся», с автоматической регулировкой возникающего по мере износа зазора между колодкой и барабаном, колёсные гидроцилиндры, что составляло немалое преимущество в сравнении с тормозами ГАЗ-21. Особенно преимущество ГАЗ-24 ощущалось при торможении с высоких скоростей: настроить передние тормоза предыдущей модели так, чтобы они срабатывали при торможении строго одновременно, было достаточно непросто, и ещё сложнее поддерживать эту равномерность в процессе эксплуатации по мере износа колодок, поэтому старую «Волгу» при экстренном торможении на скорости нередко уводило в сторону.
Работа механизма «самоподвода» основана на элементарном, но, увы, часто неверно понимаемом принципе. Поэтому на его устройстве и принципе работы придётся остановиться особо.
Разобрав рабочий тормозной цилиндр ГАЗ-24 (если вам интересно сделать это — самый простой способ это использовать сжатый воздух под давлением, только придерживайте поршни, они вылетают с достаточно большой силой !), мы увидим всего несколько простейших деталей, казалось бы, не имеющих отношение ни к какой сложной автоматике. Однако же, механизм этот работает, и работает весьма и весьма надёжно. На чём же основан принцип его действия ?
(на примере заднего цилиндра; передние устроены аналогично, но являются односторонними, с единственным поршнем)
Алюминиевый поршень 1 (здесь и далее в описании данного узла номера деталей приводятся по трёхмерной взрыв-схеме) имеет проточку для двух кольцевых уплотнительных манжет 4 в средней части и грибовидным отросток в задней части. В передней части поршня закреплён стальной носик в форме усечённого конуса с поперечной прорезью для тормозной колодки.
При сборке цилиндра в него сначала вставляют упорные кольца 5 из пружинной стали, причём в таком положении, что разрез кольца оказывается сверху, что облегчает прокачку (их вставляют в сжатом виде при помощи специального инструмента, для губок которого служат отверстия на концах кольца). Затем в цилиндр вставляют поршень, поворачивая его так, что его грибовидная часть проходит через прямоугольную часть фигурного центрального отверстия кольца, и кольцо оказывается надетым на поршень.
После этого поршень поворачивают в такое положение, при котором его становится невозможно вытащить из кольца, а прорезь в его носике занимает вертикальное положение, соответствующее ориентации тормозной колодки (именно в таком положении детали изображены на приведённой взрыв-схеме цилиндра). Поршень в таком положении может двигаться относительно кольца в продольном направлении на несколько миллиметров, но не более того (согласно руководству, рабочий ход поршня при неподвижном кольце — 1,9...2,06 мм).
Кольца в обычном состоянии имеют несколько больший диаметр, чем диаметр цилиндра, поэтому ходят внутри него с большим усилием — для того, чтобы сдвинуть их с места, необходимо приложить усилие величиной не менее 60 кг. Это больше, чем развивает стяжная пружина тормозных колодок, но меньше усилия, возникающего на поршне при хорошем нажатии на педаль тормоза. Поэтому при эксплуатации упорное кольцо может продвигаться только в одном направлении — вперёд, в сторону выхода из цилиндра. Поршень же может двигаться как вперёд, так и назад, но только на величину зазора между ним и кольцом, то есть, несколько миллиметров. Если усилие на поршне достаточно велико, то они может сдвигать своё упорное кольцо, меняя его положение в цилиндре.
Перед установкой рабочего цилиндра на автомобиль его поршни (или поршень — в передних тормозных механизмах) вместе с кольцами вручную утапливают полностью до упора, что необходимо для того, чтобы полностью свести колодки и надеть тормозной барабан.
При первом нажатии на педаль тормоза поршни под давлением тормозной жидкости начинают смещаться в сторону выхода из цилиндра, при этом полностью выбирают свой зазор с кольцами и увлекают их за собой. Они продолжают продвигаться вперёд совместно с кольцами вплоть до того момента, когда колодки тормозного механизма полностью не упрутся в барабан.
После того, как педаль тормоза будет отпущена, поршни под действием стяжной пружины колодок возвращаются назад, но лишь настолько, насколько это им позволяет текущее положение колец — тормозной механизм растормаживается. Сами же кольца при этом остаются в текущем положении, так как силы стяжной пружины не хватает для того, чтобы их сместить внутрь цилиндра, и при дальнейшей работе ограничивают рабочий ход поршня несколькими миллиметрами зазора между его грибовидной частью и кольцом.
Таким образом, тормозной цилиндр как бы «запоминает» то положение поршня, которое в данный момент требуется для срабатывания тормозного механизма, и поддерживает его в процессе дальнейшей эксплуатации, не давая ему сместиться вглубь цилиндра слишком сильно для того, чтобы его рабочего хода перестало хватать для срабатывания тормозов.
Когда колодки износятся, упорные кольца при очередном торможении опять немного сдвинутся вместе с поршнем наружу, компенсируя этот износ и тем самым «подводя» колодки к барабану, полностью отменяя необходимость делать это вручную эксцентриками.
Дополнительное преимущество такого тормозного механизма перед обычным — несколько меньшее время срабатывания: рабочий ход его поршня ограничен упорным кольцом и по величине меньше, чем в обычном цилиндре, причём эта величина остаётся всегда постоянной. В обычном же цилиндре без «самоподвода» рабочий ход поршня ограничен только положением регулировочных эксцентриков и увеличивается по мере износа колодок. Когда он становится настолько велик, что тормозной механизм без «самоподвода» перестаёт нормально срабатывать, его становится необходимо отрегулировать, «подводя» колодки к барабану эксцентриками, т.е. выполняя ту же самую операцию, которую в «самоподводящихся» тормозах выполняют кольца.
Вообще, в целом, конструкторы «Волги» выжали из её барабанных тормозов практически всё, что вообще можно было извлечь из такой конструкции: помимо дуплексной конструкции передних тормозов и весьма солидного диаметра самих тормозных барабанов, соответствующих многим иностранным автомобилям на класс выше, благодаря удачному подбору параметров тормозных механизмов удалось добиться оптимального соотношения тормозного усилия на передней и задней осях (1,5 : 1), соответствующего динамическому распределению веса между осями при экстренном торможении (60 и 40%, соответственно), что сделало сопровождающуюся заносом раннюю блокировку задних колёс практически невозможной.
В принципе, в такой системе появившийся на ГАЗ-24-10 регулятор давления в заднем контуре не был критически необходим — в отличие, скажем, от характерной для «Победы» и очень многих американских автомобилей вплоть до середины семидесятых годов системы с практически одинаковыми передними и задними барабанными тормозными механизмами с одной ведущей колодкой, действительно имеющей сильную склонность к заносу из-за ранней блокировки задних колёс и требующей ввиду этого искусственного ограничения давления в заднем контуре.
При движении же задним ходом обеспечивалось обратное соотношение — уже задние тормоза оказывались в полтора раза мощнее передних за счёт более длинной передней накладки, а также того, что при обратном направлении вращения колёс передние тормоза лишались серводействия (самозатормаживания) колодок, дополнительно прижимающего их к барабану за счёт вращения последнего.
Наиболее ощутимый не то чтобы недостаток, но во всяком случае неиспользованный потенциал — использование чугунных тормозных барабанов: к тому времени на быстроходных машинах уже широко применялись алюминиевые барабаны с оребрением для лучшего рассеивания тепла, имеющие кольцевые чугунные вставки. На фоне цельноалюминиевого двигателя и таких же картеров агрегатов это выглядит довольно странно. Судя по всему, сделано это было с целью повышения долговечности узла, так как волговские чугунные барабаны имеют очень большой запас на износ и расточку (максимальный допустимый внутренний диаметр 281,5 мм, т.е. +1,5 мм к номинальному).
Увы, но сама по себе конструкция тормозных механизмов с колодками, установленными на эксцентрических осях, представляла собой по сути пережиток 1930-х — 40-х годов, и требовала при каждой замене колодок тщательной регулировки их положения относительно барабана по зазору между ними и барабаном — процедура которой в руководствах по ремонту и эксплуатации была объяснена как правило плохо, а специальные инструменты, использовавшиеся для регулировки аналогичных тормозных механизмов на иностранных автомобилях, в отечественных источниках и вовсе не упоминаются.
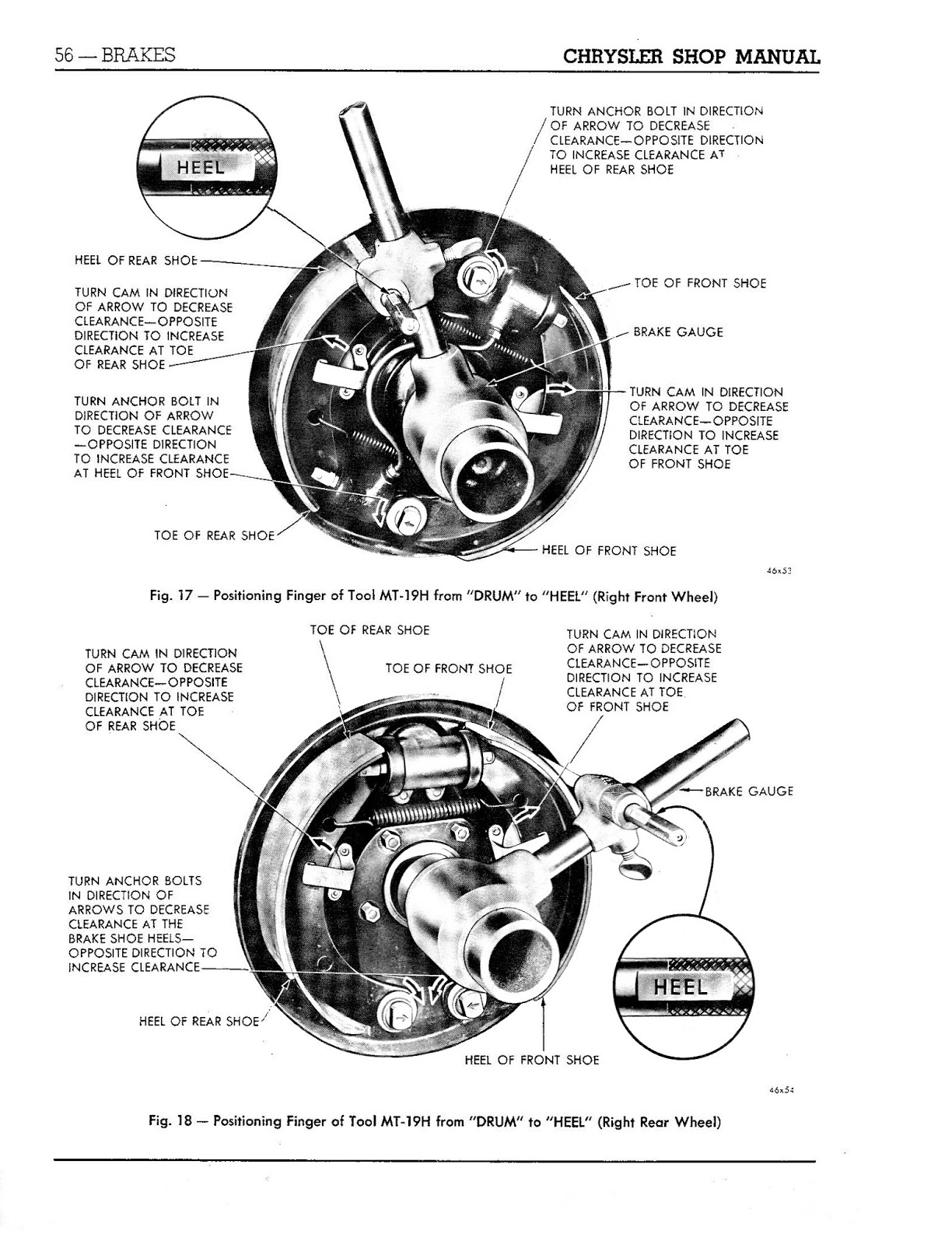
«Секретное» приспособление для выставления колодок аналогичных «волговским» тормозов типа Lockheed (использовались, в частности, на автомобилях компаний Chrysler и Willys). К сожалению, в практике отечественного автосервиса хождения не имело. Как им работать см. видео. Этим же приспособлением обеспечивается параллельность поверхности колодки тормозному барабану. Существуют также самодельные аналоги. Если делать такую приспособу для автомобилей ГАЗ, то она должна устанавливаться на шпильки ступицы для крепления колеса, т.к. у автомобилей ГАЗ ступица не снимается вместе с барабаном.
Единственным выполняемым не «на глазок» способом регулировки положения колодок, описанным в инструкции к автомобилю, является использование для контроля зазора щупа и специального регулировочного барабана с прорезью, но он работал только до тех пор, пока стоящие на машине барабаны не изнашивались, после чего регулировка по регулировочному барабану переставала адекватно работать (у иностранных автомобилей с аналогичными тормозами прорезь под щуп имели сами рабочие барабаны).
О подгонке колодок к радиусу рабочей поверхности конкретного барабана, для которой в Америке использовались специальные станочки (shoe grinder), отечественные руководства вообще не упоминают.
Смысл подгонки радиуса поверхности тормозных накладок и выставления их положения относительно барабана в том, чтобы колодка касалась барабана в первую очередь своей средней частью, а не одним из концов. В этом случае колодка будет совершать первоначальный контакт с барабаном без писка и вибрации, а затем под действием давления поршня тормозного цилиндра она немного деформируется и практически полностью прижмётся к поверхности барабана, обеспечивая максимальную площадь контакта. Поэтому имеющая правильную форму колодка должна быть обточена по радиусу немного меньше радиуса барабана, чтобы её концы имели с ним определённый зазор, причём подгонка должна вестись под конкретный барабан с учётом его износа. Подробно всё это объяснено в этом видео.
Результатом всего этого зачастую была плохая работа тормозных механизмов, писк и свист при торможении и в целом неважная репутация волговских тормозов — хотя при правильной регулировке они работают не хуже любых других «барабанов».
На других советских легковых автомобилях уже к середине 1950-х годов тормозные механизмы имели более прогрессивную конструкцию — с «плавающими» колодками, не имеющими осей и обладающими свойством в определённых пределах самоустанавливаться, что в сочетании с достаточно высокой точностью изготовления самих колодок позволило отказаться от каких-либо регулировок тормозного механизма при замене колодок, а введение «самоподвода» ещё и исключило эксплуатационную регулировку, сделав барабанные тормозные механизмы на этих машинах практически беспроблемными.
Для уменьшения усилия на педали тормоза в систему тормозов ГАЗ-24 был встроен гидровакуумный усилитель, компоновочно представлявший собой отдельный от главного тормозного цилиндра узел, который располагался в подкапотном пространстве справа по ходу движения автомобиля.

1 — тормозные механизмы передних колес; 2 — тройник; 3 — шланг ко впускному коллектору двигателя; 4 — ГВУТ; 5 — разделитель тормозов; 6 — контрольная лампа; 7 — аварийный сигнализатор; 8 — ГТЦ; 9 — тормоза задних колес;
Такая конструкция была распространена в те годы, когда усилитель воспринимался как дополнение к тормозной системе, вероятно — доступное не во всех комплектациях, а не её неотъемлемая составная часть.
ГВУТ ГАЗ-24, как и используемый на «Москвиче-412», был официальной лицензионной копией усилителя английской фирмы Girling, называвшегося Girling PowerStop (использовался на целом ряде английских моделей тех лет от недорогих «Остинов» до спортивных «Лотусов», а также австралийских автомобилях марки Holden). Такое же происхождение имеют также и некоторые другие компоненты тормозой системы ГАЗ-24 (делитель, сигнализатор).
Принцип действия ГВУТ объяснён подробно по ссылке.
Усилитель позволил значительно уменьшить усилие на педали тормоза в сравнении с предыдущей моделью, при этом сохранив очень чёткую зависимость между силой нажатия на педаль и интенсивностью торможения автомобиля. Достигалось это за счёт того, что гидровакуумный усилитель, в отличие от более привычного сегодняшним водителям вакуумного, вступал в работу лишь при достаточно сильном нажатии на педаль тормоза, когда его помощь действительно требовалась. При слабом же нажатии жидкость свободно проходила через него от главного тормозного цилиндра к рабочим, как в системе без усилителя, позволяя точно дозировать усилие при плавном торможении.
С вакуумным усилителем усилий от водителя при плавном торможении требуется меньше, но дозировать их ощутимо сложнее, а у более поздних волговских усилителей с этим вообще имелись явные проблемы — малейшее касание педали вызывало резкое замедление, в то время, как дальнейший её ход был достаточно вялым.
Также в систему тормозов включен разделитель контуров, по сути представлявший собой тройник с расположенными внутри него поршнями. Конструкция это довольно хитроумная, но всё же не обеспечивающая полноценной двухконтурной системы, как на более современных «Волгах» (начиная с ГАЗ-3102, то есть 1982 года), хотя и намного более надёжная, чем полностью одноконтурная система тормозов ГАЗ-21.
При полностью завёрнутом верхнем (прокачном) клапане центральная и боковые полости делителя не сообщаются друг с другом (кроме как через очень маленькие компенсационные отверстия, которые компенсируют изменение объёма жидкости за разделителем при изменении температуры и после начала торможения перекрываются поршнями) — вся передача усилия при торможении происходит через поршни, которые расходятся под давлением тормозной жидкости, поступающей из гидровакуумного усилителя в центральную полость, и при этом создают давление в боковых полостях, которое через трубки и шланги передаётся на колёсные рабочие цилиндры. Причём при исправной тормозной системе давление тормозной жидкости в правой и левой боковых полостях будет одинаковым.
Если же в одном из контуров появляется течь, делитель «чувствует» возникающее в неисправном контуре падение давления: при очередном нажатии на педаль поршень, отвечающий за разгерметизированный контур тормозов, под действием разницы давлений в исправном и повреждённом контурах до упора смещается в крайнее положение и остаётся в нём даже при отпущенной педали, удерживаемый остаточным давлением в системе и силой трения. В момент ухода поршня в крайнее положение водитель чувствует «провал» педали тормоза, что является сигнализацией о неисправности системы (со временем также появилась лампочка на панели приборов, загорающаяся при возникновении в контурах разницы давления).
После такого «срабатывания» делителя работать продолжает только поршень, отвечающий за исправный контур тормозов — в этом режиме можно продолжать движение до места ремонта, хотя рабочий ход педали значительно уменьшается (так как жидкость расходуется только в половине системы и педаль раньше становится «жёсткой»), а эффективность торможения падает примерно вдвое, так как тормозить будут только передние или только задние колёса.
Проблемы начинаются, если главный тормозной цилиндр уже изношен и его обратный клапан не обеспечивает требуемого остаточного давления в гидросистеме: поршень разделителя, отвечающий за повреждённый контур, при этом не удерживается постоянно в крайнем положении и при каждом нажатии на педаль всё же выталкивает часть тормозной жидкости из системы — согласно руководству по эксплуатации, в таком режиме её запаса хватает примерно на 170 нажатий педали.
При условии наличия остаточного давления, обеспечиваемого клапанами в главном тормозном цилиндре, утечек тормозной жидкости не происходит и система в теории может работать на один оставшийся контур неограниченно долго. Естественно, если при отключенном контуре тормозной системы течь возникнет и во втором контуре — машина останется вообще без тормозов (точно так же, как и машина с одноконтурной системой при течи в любой части системы).
Делитель является заметным шагом вперёд по сравнению с одноконтурной системой, так как даёт определённую страховку от внезапной полной потери тормозов, но сам принцип его работы, основанный на жёстком «отрубании» одного из контуров при малейшей течи, не нравился многим водителям, так как, к примеру, тормозная система «Жигулей» с её полностью отдельными двумя контурами, разделёнными на уровне главного цилиндра, при небольшой течи в одном из контуров какое-то время позволяла тормозить обоими контурами, пока из одного из них жидкость не вытекала полностью — внезапная потеря эффективности торможения происходила лишь при полном обрыве тормозной трубки, когда один из контуров сразу терял давление полностью, но такое в реальной эксплуатации происходит редко.
Обязательным условием нормальной работы разделителя является свободное, безо всякого заедания, перемещение его поршней.
Под действием своих пружин поршни должны легко и стабильно возвращаться в центральное положение.
Это обеспечивается в первую очередь идеальным состоянием внутренней поверхности, не разбухшими резиновыми уплотнениями (кольцами), а также — в современных условиях при использовании гликолевых тормозных жидкостей, не обладающих смазывающими и противокоррозионными свойствами — тщательным смазыванием всех внутренних деталей специальной пастой для сборки тормозных цилиндров (на полигликолевой и/или касторовой основе).
Эта конструкция хорошо работала на новой машине, с идеальным состоянием внутренностей всех гидроцилиндров, полностью исправным обратным клапаном ГТЦ и неизношенными уплотнениями, когда причиной возникновения течи могут быть только случайный выход из строя единичной манжеты в одном из рабочих цилиндров либо механическое повреждение трубок или шлангов — в таком случае она чётко сработает и предотвратит полную потерю тормозов, после чего тормозная система в кратчайшие сроки должна быть отремонтирована до полной исправности. На пожилой машине с и так уже «дышащей на ладан» тормозной системой она может принести немало проблем нерадивому владельцу, и поэтому нелюбима владельцами раздолбаных старых вёдер с неисправной и подтекающей гидравикой.
Иногда делитель вообще убирали, переходя на одноконутрную систему — делавшие это водители сохраняли надежду на то, что при небольшой течи машина продолжит тормозить практически как обычно, а момент её начала они смогут определить по изменению усилия на педали и её рабочего хода (что малореально в случае обрыва тормозной трубки или шланга, когда тормоза в одноконтурной системе пропадают сразу и полностью), а также боялись остаться вообще без тормозов при езде со сработавшим делителем в нарушение прямого указания руководства по эксплуатации о том, что данный режим предназначен исключительно для того, чтобы добраться своим ходом до места ремонта (причём их страхи умножались неполным или превратным пониманием принципа действия данного устройства).
Короче говоря — данная тормозная система хотя и работала вполне успешно для своего времени, но приносила определённые проблемы в эксплуатации и была менее надёжна, чем более современные полностью двухконтурные. Главной, если не вообще единственной, причиной её применения вместо уже существовавших на тот момент систем с вакуумным усилителем, действующим на шток педали тормоза, было (не только у ГАЗа, но и у многих других производителей автомобилей в те годы) желание сохранить унификацию по основным деталям тормозной системы с более ранними моделями (в частности — главный тормозной цилиндр был по сути взят от ГАЗ-51).
Сегодня к этому добавляются ещё и проблемы с запасными частями: в том же ГВУТе множество резиновых деталей, которые со временем выходят из строя, современных аналогов их не выпускается или они очень низкого качества, а сохранившиеся в старых гаражных запасах резинотехнические изделия как правило уже вышли из строя за истечением срока хранения. Поэтому для постоянной активной эксплуатации автомобиля остается порекомендовать лишь полностью переделать тормозную систему.
В целом, тормозная система ГАЗ-24 оказалась тупиковой ветвью эволюционного развития. ГАЗ, как и другие производители, немало экспериментировал с самыми разными типами тормозных систем и усилителей начиная с конца 50-х годов и «Чайки» ГАЗ-13, но в конечном итоге всё равно пришёл к ставшему на данный момент стандартом де факто решению — тандемные главные гидроцилиндры и вакуумный усилитель, непосредственно воздействующий на их поршни.
Кстати, на микроавтобусах РАФ, которые были построены вокруг тех же самых волговских агрегатов, для тормозов нашли более удачное решение: установили рядом два главных цилиндра, на которые через уравновешивающее коромысло передавалось усилие от педали, получив две совершенно независимые ветви гидросистемы, в каждой из которых стояло по своему гидровакуумному усилителю от «Москвича».
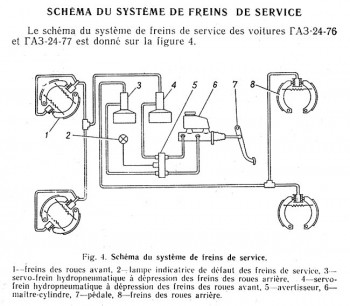
Фото © 45-45.photofile.name
В 1976 году на ГАЗ-24-76 и 24-77, поставлявшихся в качестве машинокомплектов для сборки в Бельгии, впервые появилась более традиционно устроенная система тормозов, с двухконтурным тандемным гидроцилиндром и двумя гидровакуумными усилителями — по одному на контур, видимо, основанная на наработках завода по модели ГАЗ-3101, той самой, которая впоследствии выросла в ГАЗ-3102. Таким образом, эта система стала предком всех последующих использовавшихся на автомобилях ГАЗ.
В заключение следует отметить, что в родной системе тормозов ГАЗ-24 используются тормозные жидкости исключительно на основе касторового масла — БСК. Однако в настоящее время приобрести настоящую БСК практически невозможно, поэтому остаётся либо изготавливать её самостоятельно, смешивая в равных пропорциях касторовое масло из аптеки и бутиловый спирт из магазина химреактивов, либо полностью перебрать систему, заменив в ней все резиновые детали, и перейти на современную тормозную жидкость DOT 4.
Также см. статью.
Кстати, система тормозов «классического» ГАЗ-24 очень любима владельцами «Волги» ГАЗ-21 — всё становится на «старушку» без особых переделок, совместимость полная.
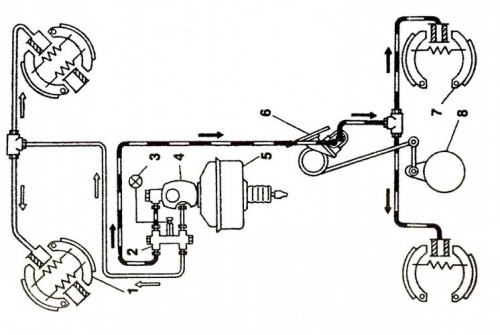
1 — передний тормозной механизм; 2 — сигнальное устройство; 3 — лампа сигнализатора неисправности; 4 — ГТЦ; 5 — ВУТ; 6 — регулятор давления; 7 — задний тормозной механизм; 8 — кожух полуоси заднего моста с кронштейном;
На ГАЗ-24-10 устанавливалась уже более современная, полностью двухконтурная система (разделение контуров на уровне главного тормозного цилиндра за счёт наличия двух тандемно расположенных камер с двумя поршнями, подключенных каждая к своему контуру), с также пролицензированным у англичан вакуумным усилителем (ВУТ), конструктивно объединенным с ГТЦ.
Усилия на педали тормоза при этом ощутимо снизились по сравнению с ГАЗ-24 однако зависимость между усилием на педали и силой торможения у ГАЗ-24-10 и последующих моделей с ВУТ стала менее внятной.
Для новичков приведу ссылку на флэшку о том, как работает ВУТ.
Также в конструкцию системы был введён регулятор давления в задних тормозах. Он был призван предотвращать ситуацию, когда тормоза задних колёс «схватывают» раньше передних, и автомобиль разворачивает на скользкой дороге (причём, видимо, этот узел появился ещё в тормозной системе позднего ГАЗ-24 — этот момент хотелось бы прояснить подробнее).
Кроме того, по имеющейся информации, на незначительную часть выпуска 24-10 ставились дисковые передние тормоза от модели ГАЗ-3102, с четырёхпоршневыми суппортами и вентилируемыми тормозными дисками.
В таком виде тормозная система оставалась по сути до самого конца выпуска «Волги», разве что с какого-то момента из неё было убрано (в общем-то, изначально непонятно что в ней делавшее) сигнальное устройство, вместо которого был установлен элементарный поплавок в крышке бачка с тормозной жидкостью, который зажигал сигнальную лампу при падении уровня жидкости, говорящем о наличии течи в системе (кажется, это произошло в период выпуска ГАЗ-31029). В 2000-е годы для «Волги» даже была разработана ABS, однако «вживую» машин, оборудованных ей, я не встречал.
Восьмицилиндровые машины имели тормоза, рассчитанные на торможение с более высокой скорости — у них были свои тормозные барабаны из материала с повышенной износостойкостью, колодки со специальными накладками из более стойкого материала, тормозная жидкость с более высокой температурой кипения. «Догонялки» на базе ГАЗ-24-10 (ГАЗ-24-34) могли иметь и дисковые тормоза спереди.
Стояночный тормоз на ГАЗ-24 принципиально отличается от двадцать-первого: он имеет привод на рабочие колодки задних тормозов — как это было ещё на «Победе». У ГАЗ-21 использовался трансмиссионный стояночный тормоз в виде маленького тормозного барабана на выходе из коробки передач с маленькими тормозными колодками внутри и механическим тросовым приводом — эта конструкция была широко распространена в практике автостроения пятидесятых — шестидесятых годов, но впоследствии от неё повсеместно отказались, примеру последовали и конструкторы ГАЗ-а.
Рычаг располагался под панелью приборов, но не слева, как у ГАЗ-21, а справа — это элемент активной безопасности, так как правая рука у большинства людей сильнее, соответственно, таким ручным тормозом гораздо удобнее тормозить при отказе рабочей тормозной системе, кроме того, им при необходимости (например, если водитель потерял сознание) может воспользоваться и пассажир.
На ГАЗ-24-10 ручник разместили между сидениями, как на «Жигулях». Соответственно, несколько упростилась конструкция (незначительно), немного повысилась надёжность, появилась возможность активно использовать ручник при вождении.