Кузов «Волги» ГАЗ-24 не только был наиболее заметным внешним отличием от предыдущей модели, но и в огромной степени определил весь набор эксплуатационных и потребительских качеств автомобиля.
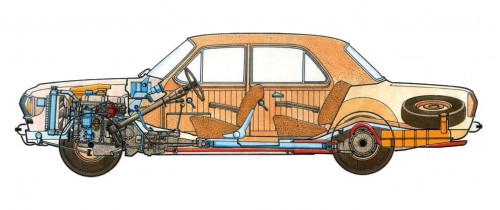
Компоновка «Волги» ГАЗ-24 была отражением последних достижений автомобилестроении по состоянию на середину шестидесятых годов.
Так же, как и в случае с «Волгой» ГАЗ-21, при создании сменившей её на конвейере модели конструкторы Горьковского завода ориентировались на американскую концепцию четырёхдверного, шестиместного автомобиля с установленными в салоне двумя широкими диванами, на каждом из которых которых могут с относительным комфортом разместиться трое взрослых людей. Это, в сочетании с иными имевшимися у конструкторов соображениями, сразу же определило основные габариты новой «Волги».
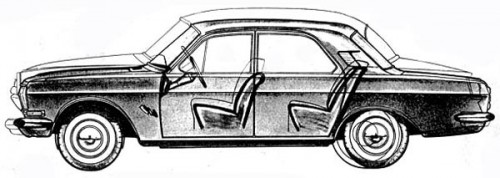
Сравнение габаритов ГАЗ-21 и ГАЗ-24. Новую «Волгу» недаром называли в прессе тех лет «автомобилем, который внутри больше, чем снаружи» — при более компактных внешних габаритах её салон по всем основным позициям был просторнее, чем у предшественницы.
В ходе работ по компоновке удалось сохранить и даже увеличить объём салона автомобиля по сравнению с предыдущей моделью, но при этом уменьшить внешнюю габаритную длину на 75 мм и, в соответствии с мировыми тенденциями, снизить высоту кузова на 130 мм, придав новой «Волге» современные, элегантные пропорции.
Габаритная ширина кузова не изменилась, так как при заданной вместимости она никак не могла быть менее 1 800 мм, но при этом применение более тонких дверей и гнутых боковых стёкол позволило ощутимо (на 25 мм в районе плеча водителя) увеличить внутреннюю ширину салона, которая, к тому же, теперь практически не менялась по всей его длине, в то время, как у ГАЗ-21 салон ощутимо сужался в районе панели приборов и спинки заднего сидения.
Ось силового агрегата ГАЗ-24 была на несколько сантиметров смещена вправо, чтобы сместить на эту же величину туннель карданного вала для создания более широкого, удобного педального узла и рабочего места водителя в целом.
Габаритная высота автомобиля достигла отметки в 1 490 мм, что было несколько больше, чем у зарубежных аналогов, но оправдано с точки зрения повышения удобства входа и выхода пассажиров в соответствии со специфическими требованиями работы в такси. Уменьшение высоты относительно ГАЗ-21 было достигнуто практически без снижения дорожного просвета, который уменьшился всего лишь на 20 мм — за счёт одновременного с занижением крыши переноса вниз панели пола, которая теперь не наваривалась поверх силовых коробов кузова, а была расположена между ними, что повлекло за собой полный пересмотр конструкции несущих элементов кузова.
Высота подушек сидений и поясной линии кузова при этом также была ощутимо уменьшена (на 70 мм), что позволило понизить центр тяжести автомобиля, улучшив его управляемость и уменьшив тряску в салоне при езде по неровной дороге, а также получить более низкую посадку и лучшую обзорность с места водителя. Кроме того, панель крыши стала плоской, что позволило выкроить несколько дополнительных сантиметров пространства над задним сидением.
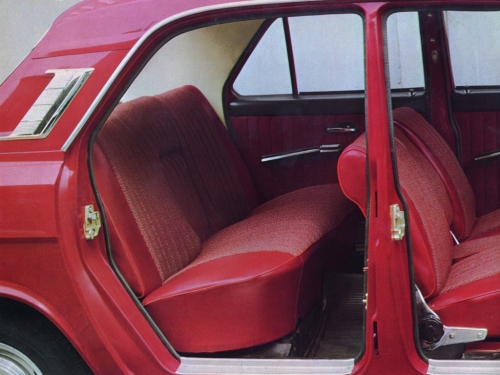
Среди особенностей «Волги» были свободная компоновка заднего пассажирского отделения и почти не вдающиеся в салон арки задних колёс.
Более низкая посадка в свою очередь потребовала большего места для ног водителя и пассажиров по длине, поэтому колёсную базу машины увеличили на 100 мм за счёт выноса ведущего моста назад. Это позволило несколько повысить плавность хода и курсовую устойчивость на скорости, ниже разместить подушку заднего сидения, вывести его за линию арок задних колес и в целом получить более свободную компоновку задней части салона, а также сделать кромку задней двери почти прямой, что существенно облегчило посадку в автомобиль и свело на нет возможность удариться лодыжкой об арку заднего колеса.
Таким образом, по основным компоновочным решениям «Волга» была вполне типичным автомобилем середины — второй половины шестидесятых годов, по габаритам и компоновке пассажирского отделения весьма близким как к американским седанам схожего размера («компактам»), таким, как Plymouth Valiant моделей 1967—1976 годов, так и к европейским моделям близкого размерного класса, вроде Mercedes-Benz S-Klasse W108. Из современных же моделей, с точки зрения объёма и габаритов салона она наиболее близка к автомобилям сегмента С по европейской классификации — или же сегмента D, но выпущенным 10-15 лет назад, что по американской классификации всё так же соответствует классу «компактных» автомобилей.
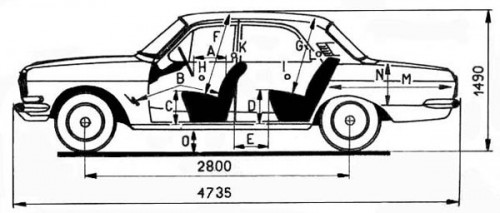
Привожу сравнительную таблицу габаритов. Все размеры даны в мм, для иномарок округлены согласно общепринятым математическим законам.
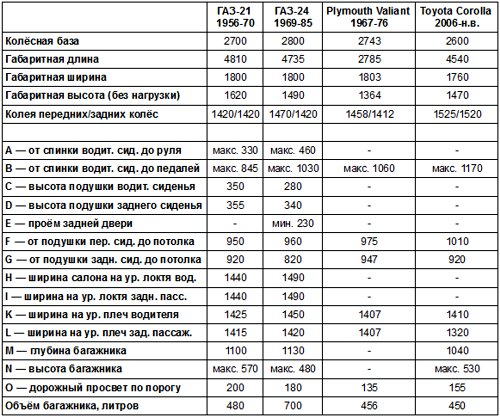
Данные по ГАЗ-21 и 24 приведены по информации из журнала Svet Motoru (ЧССР), по иномаркам — взяты из рекламных материалов производителя.
Разумеется, такая компоновка имела, с позиции сегодняшнего дня, и собственный набор недостатков.
Высота и ширина дверных проёмов «Волги» всё же были по меркам нашего времени далеко не рекордными, и по сравнению с более современными автомобилями садиться в неё водителю и пассажирам несколько сложнее. В наше время за счет увеличения наклона лобового и заднего стекол проёмы дверей стали значительно больше по ширине, а сильнее изогнутые боковые стёкла позволили ощутимо увеличить их высоту по диагонали без увеличения общей высоты автомобиля. Кроме того, кузова многих современных седанов уже стали выше, чем у «Волги», дополнительно повышая удобство посадки.
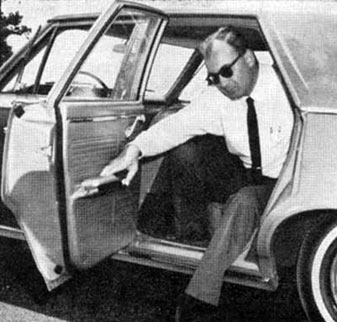
Выходить из больших, но низких американских машин тех лет было ещё сложнее, чем из «Волги» ввиду ещё больше сниженной высоты кузова.
Сочетание низкой посадки и обусловленного сравнительно большой габаритной высотой двигателя высокого капота несколько ухудшило обзорность вперёд — по некоторым данным, необозреваемая зона перед автомобилем составила 9,5 м, даже не вписавшись в требования тогдашнего ГОСТ-а, который предписывал величину не более 8 м. Естественно, в эти требования не смог бы вписаться и ни один из американских автомобилей того времени, с характерными для них исключительно длинными и высокими капотами.
Побороть этот недостаток смогли лишь в конце семидесятых и восьмидесятые годы, после массового перехода на передний привод с поперечным расположением двигателя, что позволило сделать капот ниже и более покатым. Тут, однако, проявился уже другой недостаток — такой капот оказался невидимым для водителя, сложнее стало ощущать габариты автомобиля. Видимо, оптимальный вариант в своё время предложил Chrysler на одном из своих концепт-каров начала восьмидесятых годов — низкий, покатый капот в сочетании с высокими «буртиками» по бокам, обеспечивающими хорошее чувство габаритов автомобиля. Впоследствии он был в несколько смягчённом виде использован на нескольких серийных моделях корпорации, таких, как 1981 Imperial, однако не получил дальнейшего развития, видимо из-за опасений относительно безопасности таких острых выступов для пешеходов при наезде.
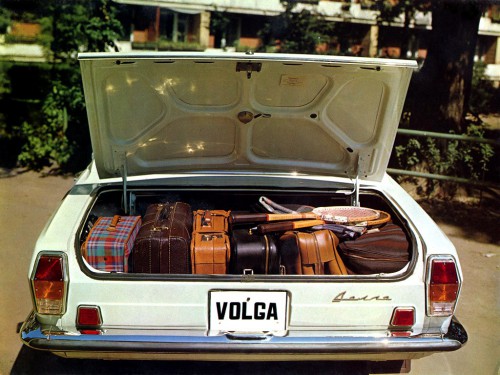
Багажное отделение «Волги» имело огромный объём и хороший доступ, но небольшая высота и высокий порог снижали удобство пользования им.
Компоновка багажного отделения «Волги», будучи вполне стандартной для того времени, сегодня также может вызвать нарекания — имея весьма немалый объём (700 литров полный / 500 полезный — против 480 литров полного объёма у ГАЗ-21), оно было очень глубоким и довольно низким, из-за чего доступ к его передней стенке и размещение багажа с большим габаритом по высоте оказались затруднены, что усугубляло высокое расположение порога багажного отсека. Кроме того, запасное колесо никак не вписывалось в низкий багажник в вертикальном положении, в котором оно находилось на ГАЗ-21 у правой стенки отсека, так что для него не нашлось никакого другого места, кроме как плашмя справа на полу багажника, где оно фиксировалось специальным винтом.
Справедливости ради стоит отметить, что в глубине багажника у ГАЗ-24 всё равно располагался агрегат обдува заднего стекла, а его огромная крышка существенно упрощала погрузку габаритного багажа, что вовсе не характерно для современных седанов, у которых крышка багажного отделения при открывании образует лишь узкую щель, через которую пролезут небольшая сумка или чемодан, не более. Кроме того, такое расположение «запаски» позволило покончить с типичной для ГАЗ-21 и характерной также для «Жигулей» болезнью — отгниванием полукруглой ниши в полу багажника для «запаски» из-за скопления в ней воды и повреждения о неровности дороги при езде по грунтовке.
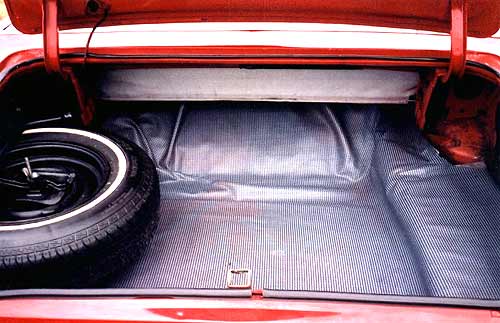
Багажник Ford Fairlane модели 1966 года по сути отличался от волговского только левым расположением запасного колеса. Оно у него точно так же прикручено к полу винтом, да и погрузочная высота так же велика.
Опять же — всё это было абсолютно типично для автомобилей того времени, и опять же — позднее с этим научились бороться, когда получили распространение кузова с поднятой вверх относительно боковины кузова крышкой багажного отделения, что позволило сделать сам багажник выше и удобнее в использовании, а «запаску» либо вернуть в вертикальное положение, либо перенести под пол, на место бензобака, «перекочевавшего» на более новых автомобилях в мало деформируемую при столкновении зону над задним мостом. Именно тогда кузова приобрели характерный слегка клиновидный силуэт.
Например, аналогичный «Волге» по компоновке Plymouth Valiant (1967 год) имел багажное отделение с полезным объёмом 14,5 куб. футов (примерно 410 литров), а созданный на его базе в начале семидесятых годов Plymouth Duster с кузовом «купе» клиновидной формы — уже от 16 до 20 куб. футов (450 — 560 литров; в зависимости от модельного года) и намного более удобное в использовании.
Именно так поступили и конструкторы «Волги» ГАЗ-3102 в конце семидесятых годов, насколько это позволяла старая конструкция кузова — разместили крышку багажника горизонтально и перенесли запасное колесо в подполье. К сожалению, на более поздних моделях «Волги» от этого решения пришлось отказаться из-за невозможности унифицировать панель пола с универсалом, для которого расположение бензобака над задним мостом было совершенно неприемлемо.
Начиная говорить о конструкции, следует в первую очередь отметить, что кузов «Волги» ГАЗ-24 был первым из спроектированных на ГАЗ-е несущих кузовов, который не имел преемственности с идущей ещё от «Победы» (и в целом соответствующей автомобилям конца тридцатых годов) общей схемой, у которой длительная практика эксплуатации выявила ряд существенных недостатков с точки зрения долговечности.
Очень часто возникает дискуссия на тему, какую конструкцию имеет кузов ГАЗ-24 — рамную или безрамную? Ответить на этот вопрос будет далеко не так просто, как может показаться на первый взгляд. Наиболее корректным ответом будет такой: кузов «Волги» — самонесущей конструкции с установленной в передней части приварной подмоторной рамой, несущей переднюю подвеску и силовой агрегат.
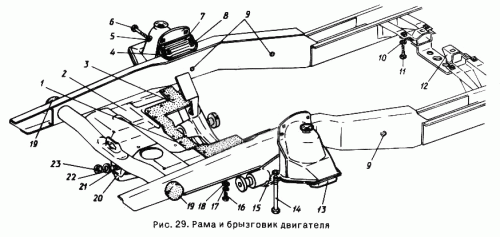
Хотя кузов «Волги» и был несущим, короткая рама у неё также имелась.
Эта укороченная рама имеет вполне традиционную конструкцию — два параллельных друг другу продольных лонжерона и четыре поперечины (первая — в виде отрезка круглой трубы, вторая — кованая балка передней подвески на болтах, третья — заднее крепление коробки передач, четвёртая — приваренный к полу кузова штампованный усилитель). Лонжероны её доходят практически до середины автомобиля, плавно утончаясь и переходя в коробчатые усилители пола пассажирского салона, пока полностью не исчезают примерно под сидением водителя. Крепятся они к кузову сваркой, в отличие от «Победы» и «Волги» ГАЗ-21, у которых крепление подмоторной рамы было разъёмным — на болтах. Для более равномерного распределения усилий на кузов к раме привариваются два подкоса, соединяющие её с щитом моторного отсека.
Таким образом, по сравнению, скажем, с «Жигулями» или современными легковыми автомобилями рама у «Волги» всё же есть, правда, короткая и неподвижно соединённая с кузовом. Именно так и обозначается так называемый «подрамник» во всей официальной документации ГАЗ-а, руководствах по ремонту и каталогах запасных частей.
Вот такое вот интересное сочетание: кузов несущий, но рама — всё равно есть.
Задняя оконечность кузова «Волги» была уже полностью несущей: задние лонжероны представляют собой простые усилители пола в виде приваренных к нему снизу П-образных профилей. В средней же его части роль несущих элементов играют короба (внутренние пороги, расположенные под дверными проёмами) и внешние пороги, также приваренные к полу кузова.
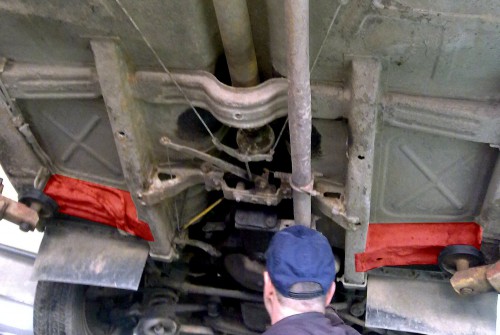
Хорошо видна сравнительно простая продольно-поперечная структура силовых элементов кузова ГАЗ-24. Раскосы пола выделены красным.
Лонжероны соединяются с коробами поперечными элементами, которые у нас именуются раскосами пола, а в английском языке обозначаются как torque boxes.
Такая конструкция несущих элементов кузова, в принципе, была типична для автомобилей того времени, как американских, так и европейских, но в Европе она уже начала вытесняться полностью несущими кузовами, как у «Жигулей», у которых лонжероны подрамника как самостоятельные элементы отсутствовали, а вместо них использовались накладные усилители пола и брызговиков передних крыльев П-образного сечения.
Однако именно наличие вот этих массивных раскосов ставит «Волгу» несколько особняком, поскольку, если рассматривать несущие элементы её кузова как единое целое, получится конструкция, весьма близкая к раме так называемого периферийного типа, интегрированной непосредственно в кузов: те же самые широко расставленные в средней части кузова продольные несущие элементы, между которыми «подвешен» пол пассажирского салона, которые спереди и сзади через «торк-боксы» переходят в лонжероны.
Это не случайно, просто это — наиболее совершенный тип несущей структуры с точки зрения обеспечения наибольшего полезного пространства салона, вне зависимости от того, имеет ли автомобиль отдельную раму или аналогичные ей элементы, интегрированные в конструкцию самого кузова. И преимущество здесь состоит именно в том, что в средней части кузова продольные несущие элементы охватывают весь салон по периметру, создавая вокруг него монолитный жёсткий каркас, но при этом не отнимая у него полезное пространство; поперечные же элементы расположению водителя и пассажиров не мешают, так как располагаются под передним и задним сидениями.
У американских машин с несущим кузовом эти элементы усиления часто отсутствовали, что делало кузов ощутимо менее жёстким и живучим; например, из безрамных «Фордов» «торк-боксы» присутствовали у единственной модели Fairlane (которая была ощутимо крупнее «Волги»), на которой они были предусмотрены в связи с увеличившимися при растягивании платформы Ford Falcon нагрузками (при этом их очень часто ставят на автомобили этой платформы, особенно «Мустанги», в виде тюнинга, т.е. жёсткости реально не хватает).
Примерно такая же конструкция силовых элементов днища, без раскосов пола, использовалась и на «Москвиче-412» — а вот на «пирожках» (пикапах) они как раз были, как и другие усиления кузова.
Усиленную конструкцию имели и многие другие элементы несущей структуры кузова «Волги». Так, пороги ГАЗ-24 (сечение Г-Г на чертеже) — это не просто коробчатые профили (как, к примеру, у «Москвича-402»), и даже не короб с наваренной на него снаружи декоративной накладкой (как у «Победы» и ГАЗ-21, а также «классических» «Жигулей»); это довольно сложная трёхмерная конструкция со вваренными внутрь короба распорками-усилителями, имеющими перфорацию для улучшения вентиляции. Внешние же «пороги» дверей — это на самом деле не сами пороги кузова, а деталь, которая в официальной номенклатуре обозначается как «накладка порога» — она выполняет чисто-декоративную функцию (и с технологической точки зрения является часть проёма двери боковины, а не силового каркаса днища).
Аналогично, и стойки крыши также представляли собой сложные профили со вваренными усилителями. В целом, по конструкции кузова «Волга» ГАЗ-24 является, пожалуй, одним из наиболее сложных отечественных автомобилей, что является прямым следствием заложенного в него высокого ресурса, рассчитанного на работу в такси.
Всё это позволило существенно усилить кузов без излишнего завышения массы автомобиля.
Конструкция кузова обеспечила «Волге» и весьма неплохой для своего времени уровень пассивной безопасности. В районе моторного щита подрамник образовывал вместе с двумя подкосами жёсткий силовой узел в виде треугольника, обеспечивающий эффективную передачу энергии удара на кузов, а длинные лонжероны обеспечивали энергопоглощающую деформацию при ударе. Появившаяся на новейших европейских автомобилях во второй половине семидесятых — начале восьмидесятых более современная конструкция силового набора кузова, с деформирующимися в виде «гармошки» прямоконусными лонжеронами, S-образно изгибающимися под моторным щитом и плавно «уходящими» в короба, конечно, лучше, но на фоне автомобилей конца шестидесятых и первой половины семидесятых годов «Волга» выглядела вполне достойно.
Кстати, стоит отметить, что на американских автомобилях конструкция силового набора долгое время отставала от европейских образцов. Например, разработанные в восьмидесятые годы крайслеровские платформы LH и JR, на последней из которых была построена «Волга-Сайбер», в этом отношении не так уж далеко ушли от автомобилей шестидесятых и семидесятых — тот же продольно-поперечный набор силовых элементов, те же прямые лонжероны.
Что касается прочности и жёсткости кузова, то технический прогресс в этой области никогда не стоит на месте — по жесткости кузова на скручивание в пределах колёсной базы «Волга» ГАЗ-24 примерно вдвое превосходила разработанную за двадцать лет до неё «Победу» (9 000...10 000 Н·м/град. против 4 600) и, в свою очередь, примерно на столько же уступала автомобилям того же класса, созданным 20-30 лет спустя (Volkswagen Passat B5 1996 года — 24 000 Н·м/град.).
По сравнению с «Волгой» ГАЗ-21, кузов новой модели был существенно более жёстким, долговечным и безопасным, несмотря на меньшую массу и толщину металла, что было достигнуто за счет использования более прочной и совершенной несущей системы, а также приварных, а не крепящихся на винтах, задних крыльев, брызговиков крыльев, щитков радиатора и так далее, которые все вместе образовывали цельную сварную конструкцию, в которой каждая деталь работала на увеличение общей прочности и жёсткости.
Штамповка и сварка кузовных панелей, всё ещё оставаясь достаточно грубыми по мировым меркам, всё же сделали большой шаг вперёд по сравнению с ГАЗ-21, то же самое касается и задействованных в изготовлении автомобиля технологий — тяжёлый и малопроизводительный ручной труд всё больше вытеснялся высокопроизводительными автоматизированными технологическими процессами, хотя в этом уже наметилось отставание от «Москвича» и АвтоВАЗ-а (которые использовали иностранную технологию производства и в значительной степени выпущенную за рубежом оснастку: ВАЗ — с самого начала, АЗЛК — после реконструкции, проведённой в конце 60-х годов с участием фирмы Renault).
Собственно, большие шаги в этом направлении были сделаны ещё в ходе выпуска ГАЗ-21 — в частности, был совершён переход на цельноштампованную боковину кузова вместо сваренной в кондукторе из пяти отдельных деталей (передней, задней и центральной стоек, порога пола и рейки крыши) на «Победе» и ранних выпусках «21-й», у которой геометрия «плавала» в широких пределах. Однако в полной мере внедрить появившиеся к тому времени в данной области технологические новинки можно было лишь на принципиально новом автомобиле.

Основные сборочные единицы кузова ГАЗ-24: 1 — основание кузова (пол); 2, 3 — правая и левая боковины; 4— узел переднего окна; 5 — узел заднего окна; 6 — крыша
Окончательная сборка кузова ГАЗ-24 осуществлялась из 6 крупных предварительно подсобранных узлов (см. рисунок выше) — панели пола, двух боковин, рамок лобового и заднего стекла и крыши (без учёта навесных элементов, крепящихся на болтах). Для сравнения, у «Победы» кузов собирался из 11 узлов, а у «Волги» ГАЗ-21 на заключительном этапе её выпуска — из 7. Кузов автомобиля ВАЗ-2101 «Жигули» также собирался из 6 крупных узлов, то есть, в этом плане разработанная на ГАЗе технология была не менее совершенна, чем фиатовская (правда, у «Жигулей» сюда входили и приварные передние крылья — что имело как плюсы, так и минусы с эксплуатационной точки зрения).
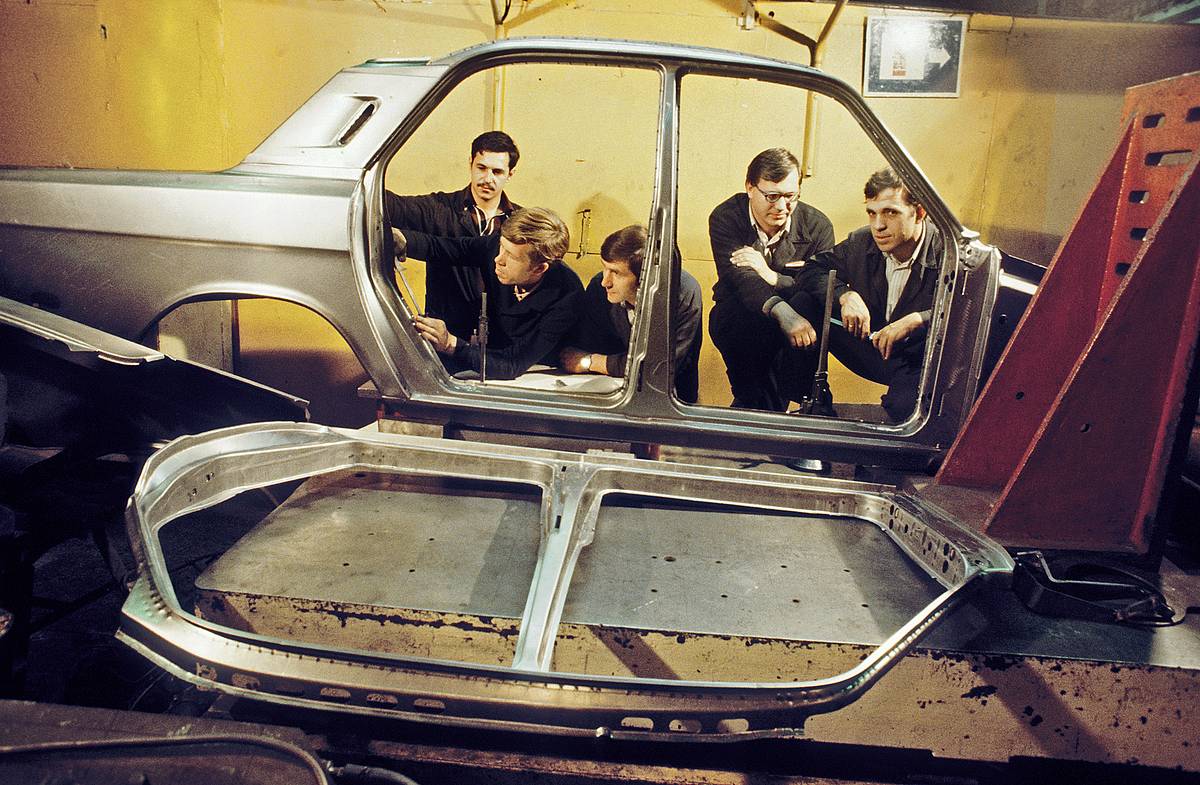
С самого начала деталь, образующая проёмы дверей, у ГАЗ-24 была цельноштампованной, что позволило значительно снизить трудоёмкость изготовления кузова и одновременно повысить точность соблюдения его геометрии. Фото В. Войтенко (Фотохроника ТАСС).
Меньшее число сборочных единиц в данном случае означает меньшее число операций по сопряжению отдельных кузовных панелей при сборке, каждая из которых создаёт возможности для отклонения от заданных размеров. Собирать кузов из небольшого числа крупных панелей быстрее и выгоднее, чем из большого числа мелких, хотя и сложнее в технологическом плане. При этом следует помнить, что у «Победы» и «21-й» «телевизор» передка и задние крылья тоже были навесными деталями — то есть, фактически общее число осуществляемых при сборке автомобиля сопряжений было ещё больше.
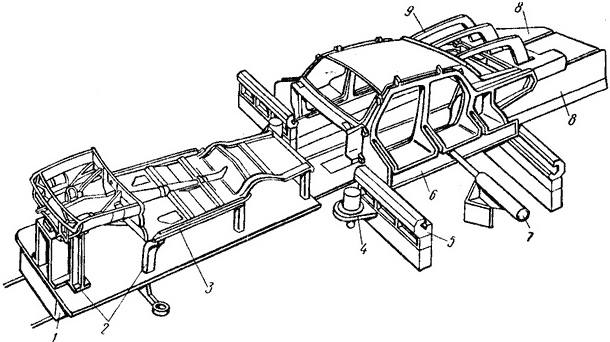
Главный кондуктор для сборки и сварки кузова ГАЗ-24 — «сердце» использовавшейся для его изготовления производственной оснастки: 1 — тележка кондуктора, 2 — узлы фиксации основания кузова, 3 — основание кузова, 4 — пневмопривод тележки, 5 — направляющие подачи боковин кузова, 6 — салазки с узлами фиксации левой и правой боковин, 7 — гидроцилиндр, 8 — чугунная плита основания, 9 -прижимное устройство проёма заднего стекла. Всего данное приспособление имело 95 опорных точек фиксации и 60 прижимов, в основном с пневматическим приводом.
При изготовлении кузова ГАЗ-24 использовалось шесть стационарных кондукторов, включая несколько сравнительно простых, предназначенных для подсборки отдельных узлов — основания кузова, боковин и т.п., и весивший 12 тонн главный кондуктор, служивший для окончательной сборки (см. рисунок выше), работа которого была в значительной степени механизирована за счёт пневматических и гидравлических сервоприводов (для сравнения — при сборке кузова «Победы» практически все операции в главном кондукторе осуществлялись вручную, по методу «раз-два-взяли»). Особое внимание было уделено упрощению технологических операций и снижению трудозатрат — в частности, рациональному расположению фиксирующих приспособлений и уменьшению их размера и массы.
Сборка кузова осуществлялась в следующей последовательности. Сначала в фиксирующие устройства кондуктора устанавливались проём заднего окна, боковины кузова и проём переднего окна. Затем вместе с фиксирующими устройствами их при помощи гидропривода подавали в рабочее положение и приваривали к ним крышу. После этого внутрь кондуктора подавалась тележка, на которой было закреплено основание кузова включая подмоторную раму, которая приводилась в рабочее положение поднятием на 200 мм за счёт винтового механизма с электроприводом. Сваривая основание кузова с боковинами и проёмами стёкол по выступающим фланцам, получали готовый к дальнейшим технологическим операциям кузов в сборе без навесных деталей.
Общее число точек сварки, выполняемых в главном кондукторе, достигало пяти сотен, большинство из них выполнялось вручную сварочными пистолетами (т.е. общее количество точек было намного больше, так как приведённое число не учитывает точки, выполненные до окончательной сборки кузова в главном кондукторе).
Такая технология была не самой передовой для того времени и сравнительно малопроизводительной — в час бригада из трёх человек могла собрать не более трёх-четырёх кузовов — что, впрочем, вполне соответствовало масштабам выпуска «Волги».
Для сравнения, использовавшийся на ВАЗе подвижный кондуктор проходного типа с челночной загрузкой позволял сваривать до 100 кузовов за одну смену (если принять длину смены за стандартные 8 часов — получается производительность в 12...13 кузовов в час), при этом многие сварочные швы выполнялись многоэлектродной машиной, которая за один технологический приём ставила сразу 96 сварочных точек — при их общем числе в 278. На АЗЛК сборка и сварка кузовов осуществлялись на механизированной поточной линии производительностью 52 кузова в час. Однако, эти заводы по проектному объёму выпуска автомобилей превосходили ГАЗ во много раз, так что сравнивать их технологические процессы напрямую некорректно — они изначально создавались под различные масштабы производства.
Кстати, это — одна из составляющих ответа на вопрос о том, можно ли было увеличить выпуск «Волги» в два / три / несколько раз ? В теории — можно, но на практике для этого фактически требовалось создать для неё «с нуля» полностью новую технологию производства, адаптированную для таких масштабов выпуска — как это было сделано с «Москвичём» 408/412 в ходе реконструкции завода при участии французов.
Ту же пропускную способность главного сварочного кондуктора без переделки всего техпроцесса штамповки, сборки и сварки кузовов по образцу тех же ВАЗа или АЗЛК увеличить не получилось бы. И такие проблемы возникали бы при попытке масштабирования объёмов выпуска не только на каждом этапе производства на самом ГАЗе, но и на каждом предприятии-смежнике.
На практике даже в середине девяностых, работая с полным напряжением всех сил в три смены по 6 дней в неделю, с тотальным проседанием качества за счёт максимально возможной экономии материалов и упрощения всех технологических процессов, ГАЗ сумел нарастить выпуск «Волги» лишь с 65 до 124 тысяч автомобилей в год — т.е. даже близко не приблизился к проектным 500-600 тыс. автомобилей в год АвтоВАЗа. При том, что спрос на продукцию завода намного превышал предложение.
Кузовные зазоры «Волги» никогда не отличались особым изяществом, но во всяком случае вплоть до второй половины восьмидесятых были ровными и по величине не отличались от других советских автомобилей того же поколения — 5±1 мм в среднем по чертежу, что и по мировым меркам в те годы, до внедрения сборочных роботов нового поколения, было нормальным значением за пределами немецкого автопрома, который за счёт качества рабочей силы и производственной дисциплины уже в те годы мог собирать кузова с существенно меньшими зазорами, чем, скажем, на массовых американских моделях. У сегодняшних машин эта же величина составляет, как правило, 3±1 мм у производителей первого эшелона и 4±1 мм у второго-третьего — точность штамповки и возможности по сопряжению сложных криволинейных поверхностей кузовных панелей за последние десятилетия выросли на порядок.
Антикоррозийная обработка металла кузова (фосфатирование плюс анафорезный грунт, наносимый электроосаждением) была также улучшена и находилась на уровне своего времени (и постоянно совершенствовалась в процессе выпуска), хотя и в таком виде вызывала нарекания у эксплуатационников — увы, в суровом климате большей части Союза при постоянной круглогодичной эксплуатации без дополнительной обработки уже на четвёртый-пятый год оперение и двери «Волги» прогнивали до сквозных дыр (как и большинство иномарок нижней-средней ценовых категорий, не имевших с завода подкрылков и хорошей антикоррозийной обработки скрытых полостей ингбиторами коррозии).
Относительно дополнительной антикоррозийной обработки, информация противоречива. В книге по ремонту 1975 года указано, что днище, колёсные арки и наклонная часть моторного щита покрываются на заводе «ровным слоем специальной мастики № 579 или № 213 вручную или способом пульверизации», также мастикой покрывались внутренняя часть дверей и брызговиков передних и задних крыльев.
Однако обнаружить такую обработку удаётся не на всех машинах, как минимум один известный мне автомобиль 1983 года выпуска никаких следов мастики на днище не имел — днище на нём было защищено только слоем грунта и краски (видимо, к концу выпуска модели качество антикоррозийной обработки, как и всего остального, начало снижаться) — и, соответственно, по состоянию на начало 2010-х гг. оно было уже немного ржавым, в особенности по выполненным внахлёст сварным швам, которые с завода также не герметизировались (но не гнилым, без сквозной коррозии). Разумеется, автомобиль эксплуатировался исключительно летом, что для частных автомобилей было в те годы скорее правилом, чем исключением.
Впрочем, даже нанесённое на заводе покрытие битумной мастикой играло роль в первую очередь шумоизоляции, а в качестве антикора она работала в течении 2-3 лет после нанесения, после чего обработку требовалось повторять, так как мастика теряла эластичность и начинала постепенно отслаиваться. Более прогрессивных пластизольных мастик (на основе дисперсии частиц поливинилхлорида в пластификаторе), которые использовались АвтоВАЗом с середины 1980-х годов, ГАЗ на тот момент не применял — не говоря уже о материалах на основе синтетического нитрилового каучука, применявшихся в 80-е годы для защиты днища иномарок (со сроком службы 10-15 лет).
Вообще, в мире эволюция средств для герметизации нижних поверхностей кузова выглядела примерно таким образом:
- Материалы на основе сланцев, битума и резинобитумных композиций — примерно до конца 1970-х гг.
- Материалы на основе пластизолей (1970-е — 80-е гг.)
- Материалы на основе синтетического каучука — примерно с середины 1980-х гг.
- Материалы на основе полиуретана — 1990-е — начало 2000-х гг.
- Материалы на основе силан-модифицированного полиуретана (MS-полимеров) — примерно с середины 2000-х — начала 2010-х гг. используются ведущими производителями (Mercedes-Benz, BMW, VAG и т.п.)
Как видно, технологии в данной области — как и в областях подготовки кузова к окраске, способов грунтования, а также самих грунтов и эмалей — не стояли на месте, и коррозионная стойкость современных машин, даже с не оцинкованными кузовами, далеко не случайна (и уж конечно не является следствием использования некоего мифического «супер-пупер» железа, якобы не ржавеющего самого по себе; наоборот, «высокопрочные» стали, из которых в значительной степени выполнены кузова современных автомобилей, отличаются высокой склонностью к коррозии и требуют очень тщательной обработки металла — без современных достижений в этой области их использование в автомобилестроении едва ли стало практически реализуемым).
Судя по жалобам работников таксопарков — см. к примеру здесь — никакой антикоррозионной обработки скрытых полостей на ГАЗе не проводилось даже в конце 70-х годов, хотя такой способ защиты от коррозии к тому времени уже был известен и применялся как за рубежом, так и в СССР. Так что при круглогодичной эксплуатации долговечность кузова «Волги» полностью зависела от того, была ли произведена эксплуатантами дополнительная защита от коррозии, и если да — то насколько тщательно.
Как писалось в №3 журнала «Автомобильная промышленность» за 1977 год,
За рубежом многие автомобильные фирмы для дополнительной защиты кузовов автомобилей и автобусов вводят в полости кузовов специальные ингибирующие составы. Эта операция осуществляется как в условиях производства, так и на станциях технического обслуживания... На заводах фирм Альфа-Ромео (Италия), Даймлер-Бенц и БМВ (ФРГ), Форд (Бельгия), Икарус (Венгрия) составы для дополнительной защиты наносятся на основных линиях сборки автомобилей, для чего в конструкции кузова предусматриваются специальные технологические отверстия. В нашей стране подобные работы проводятся на Волжском автозаводе им. 50-летия СССР и на станциях технического обслуживания, созданных этим и другими заводами отрасли при участии ЭКТИавтопрома.
Разумеется, толковые владельцы сразу же либо гнали машину на СТО для фирменной антикоррозийной обработки, либо сами заливали в полости кузова «Мовиль» или масляный антикор — необходимые для этого технологические отверстия заводом предусмотрены были, им же была разработана технологическая карта обработки кузова. При её периодическом повторении даже кустарная антикоррозионная обработка была достаточно эффективна. Без дополнительной обработки же, как уже указывалось, кузов «Волги» до появления сквозной коррозии служил при круглогодичной эксплуатации 4-5 лет.
Только в 1980-е годы, уже в самом конце выпуска модели ГАЗ-24, внутренние полости кузова стали с завода обрабатываться препаратами типа «Мовиля» группы МЛ-2 — НГМ-МЛ, Мольвин, Мольвин-МЛ. Но и они работали в течение 2-3 лет, после чего требовалась повторная обработка.
Не было и специальной обработки сварных швов и выполненных внахлёст стыков кузовных панелей шовным герметиком, повсеместно используемым в наши дни, так что незначительная (но неприятная с эстетической точки зрения) коррозия в районе сварных швов начинала проступать довольно быстро, если только они не были пропитаны «Мовилем» или схожим составом сразу же после покупки автомобиля (как надо делать, чтобы этого не происходило — см. здесь и здесь). Отчасти её роль играла мастика, наносившаяся на днище и внутри багажника, а также напыляемая пластмасса ТПФ-37 (пришедшая на смену свинцово-оловянному припою), но к примеру фланцы дверей не были защищены с завода ничем, кроме слоя краски.
Не обошлось и без чисто конструктивных просчётов, ведущих к повышенной склонности отдельных частей кузова к коррозии. Так, типичным местом появления ржавчины являются развитые фланцы дверей, в особенности — их нижние части и углы, постоянно находящиеся в сырости. Главная причина здесь — именно конструктивная: фланец двери образован тремя слоями металла, внутренней панелью двери и завальцованной вокруг неё наружной, и, таким образом, весь фланец представляет собой двух-трёхслойный «бутерброд», внутрь которого грунт практически не попадал, из-за чего металл оставался по сути не защищённым от коррозии, и при этом — был открыт для попадания влаги как снаружи, так и изнутри двери, что создавало вольготные условия для развития ржавчины:
В этих местах ржавчина есть даже у машин, в целом лишённых значительных проблем с кузовом, что бывает весьма обидно в случае хорошо сохранившейся родной краски. Хотя, конечно, в своё время данный дефект носил сугубо косметический характер, так как на эксплуатационных качествах автомобиля никоим образом не сказывался. Более-менее успешно бороться с ним позволяла немедленная после покупки автомобиля обработка внутренней полости двери и наружных стыков панелей легкопроникающим антикором, который пропитывал металлический «бутерброд» и плотно его закупоривал от попадания воды. В современных условиях также крайне рекомендую перед окраской все загибы и стыки фланцев дверей промазывать кузовным полиуретановым герметиком (не обязательно «колбаской», как это сделано на современных автомобилях — вполне достаточно тонкого слоя, аккуратно нанесённого кистью и под краской почти незаметного; главное — чтобы он герметично перекрывал все щели и стыки).
Инетерсно, что у ГАЗ-21 фланцы дверей были конструктивно схожи, но имели намного меньшие размеры, что, видимо, сказывалось на их коррозионной стойкости; кроме того, вероятно, и металл дверей был потолще, так что ржавчина не так быстро выбиралась наружу:
Нельзя не отметить то внимание, которое было уделено создателями автомобиля мелочам, ощутимо влияющим на удобство его эксплуатации, обслуживания и ремонта.
Так, капот имел подпружиненные петли, которые облегчали открывание и фиксировали его в открытом положении — многие бюджетные иномарки и сегодня вместо этого предлагают водителю поддерживающую капот неудобную откидную стойку.
Крышка багажника также удерживалась в открытом состоянии торсионами, которые, будучи исправны и отрегулированы, с силой открывали её при простом повороте замка, что очень удобно, к примеру, если у вас заняты руки — современные газовые подпоры этого часто не обеспечивают, и водителю приходится либо класть свою ношу на землю, либо проявлять чудеса акробатики, одновременно обнимая поклажу одной рукой и поднимая крышку багажника второй.
Сам замок багажника также был решён очень удачно — он имел поворотную фишку в виде «барашка», поворот которой в любой момент открывал отпертый ключом багажник — такая система выгодно отличалась от утапливаемой кнопки ГАЗ-21 и «Жигулей» своей вандалостойкостью. Лючок бензобака также имел замочек, предотвращающий кражу бензина или попадание в бензобак посторонних предметов.
В кузове имелось две розетки с напряжением 12V — одна в салоне и одна под капотом, к ним можно было подключить не только прилагавшуюся к каждому автомобилю лампу-переноску, но и всевозможную 12-вольтовую бытовую технику.
Двери и передние крылья «Волги» крепились на винтах, а не сварке, что существенно облегчало кузовной ремонт автомобиля.